What is an ARA?
You probably already leverage common methodologies such as Failure Modes and Effects Analysis (FMEA), Risk-Based Inspection (RBI), or Reliability Centered Maintenance (RCM) to manage the reliability of your facility. However, how confident are you in the forecasted reliability of your facility? Are you able to use your data to drive reliability decisions for your entire facility?
With Quantitative Reliability Optimization (QRO), your facility can take the next step in achieving facility-wide reliability objectives. QRO is a new dynamic reliability approach that bridges the existing first principle’s reliability models with new data science, multi-variate analysis, and system-based optimization. This combination improves facility performance, balancing availability, process safety, and spending performance.
QRO is comprised of four elements: Asset Risk Analysis (ARA), the Lifetime Variability Curve (LVC), Forecasting System Availability, and Reliability Simulation and Performance Optimization. The cornerstone of QRO is the ARA.
ARAs integrate industry-leading engineering principles, field execution tasks, and measured data to quantify uncertainty and optimize all tasks and spending at a facility. ARAs create a causal link between assets’ functions, failure modes, and failure mechanisms to identify the reliability and maintenance tasks needed to mitigate failures and reduce uncertainty. As a result, you will be better able to streamline the deployment of limited resources and help facilities achieve a strong return on investment.
Typical reliability methodologies measure various asset classes through different programs, which can lead to wasted spending and unmanaged risk. ARAs enable a consistent, data-driven analysis across different asset types in a single platform. ARAs are driven by critical reliability data, giving you better insight into the failure risk of their assets and enabling them to shift to a more proactive approach to reliability and maintenance.
By evaluating assets consistently and quantitatively in a single platform, facility leaders can now effectively compare risks or prioritize resources across different asset classes.
How Does an ARA Work?
First, an ARA analyzes an asset’s function and specific performance requirements. Next, failure modes and potential failure mechanisms are evaluated, and the ARA establishes causal links between the two. The ARA then analyzes critical reliability data to determine the basis for the asset’s probability of failure. Next, the Consequence of Failure (COF) scenarios is documented for production impacts, HSE risk, and repair and replace costs, and links the data and maintenance tasks needed to prevent the failures from occurring.
As a result, an ARA implementation gives facilities better insight into how they can use already available data to implement a more proactive approach to maintenance and reliability.
Example of an ARA
A fin fan heat exchanger is comprised of both fixed and rotating pieces such as header boxes, fans, and motors. Today, these components are managed by RBI and RCM programs separately. RBI is typically more quantitative while RCM is more qualitative. As a result, facility leaders often have a hard time prioritizing limited resources across asset types to prioritize what tasks need to be completed when. Furthermore, the execution of these tasks is typically siloed and inefficient resulting in wasted man hours and more time spent in the field collecting data.
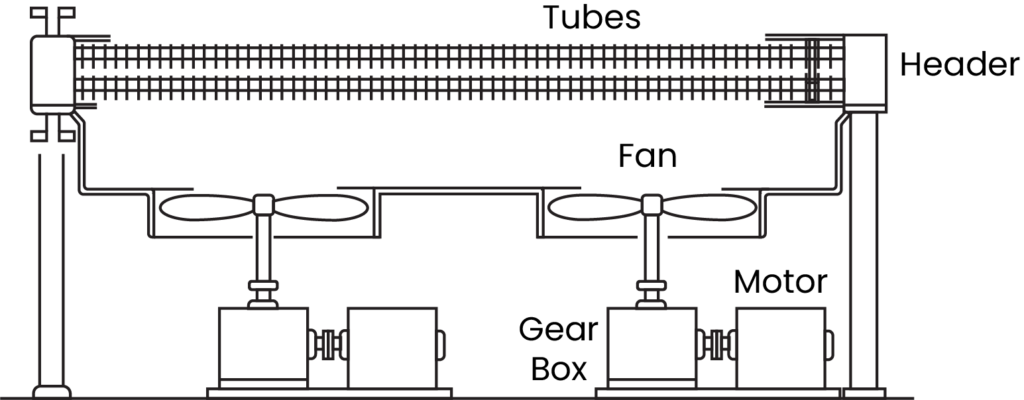
Leveraging an ARA, facility leaders can see all of the failure modes and mechanisms for both the fixed and rotating components of the exchanger. Additionally, the ARA links the maintenance and inspection tasks needed to mitigate the failure modes. These links create the foundational data infrastructure to optimize using more complex analyses such as machine learning and artificial intelligence.
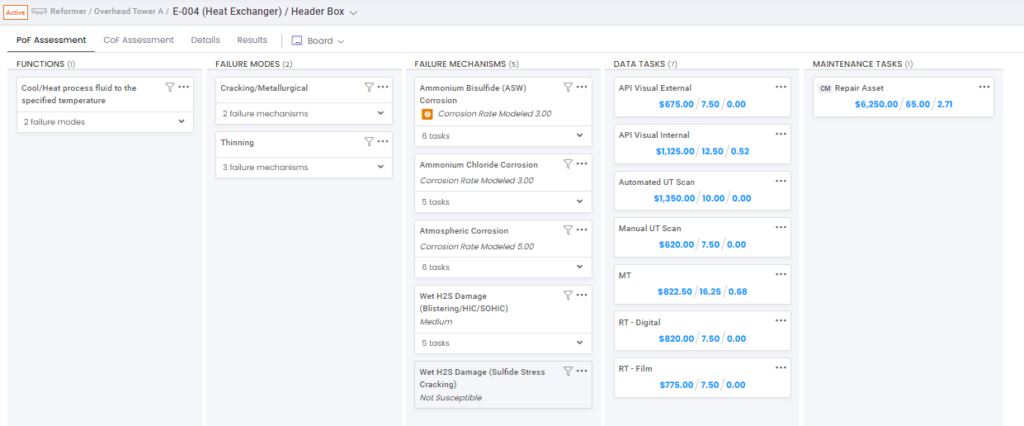
Benefits of an ARA
With ARAs, facilities can determine where they can optimize their reliability and maintenance budgets and can put their money toward the best use. Additional benefits include:
- Assess all asset types using the same methodology and quantitative results, breaking down silos in reliability and enabling effective comparison and prioritization of risks and asset management plans across all asset classes.
- Clearly understand causal links between asset functions, failure modes, failure mechanisms, critical reliability data, and field execution tasks, laying the foundational framework for any successful reliability program.
- Creating a framework to understand the benefit to cost of every task for all assets in your facility and determine total cost of ownership for all assets in your facility.
- Ability to rank reliability and maintenance tasks based on the likelihood of failure and the amount of uncertainty around that probability
Stay in the know.
Providing data-driven insights, perspectives, and industrial inspiration from the forefront of the reliability transformation.