An Introduction to Risk-Based Inspection
For complex processing industries, knowing where to focus inspection spend, when to perform inspections, and which methods will provide the most confidence in understanding an asset’s current state is crucial. This information helps facility leaders decide how to reduce loss of containment events and prioritize inspection budgets. Risk-Based Inspection (RBI) is a proven asset integrity management method for prioritizing and optimizing inspection activities, identifying and understanding risk drivers, and creating effective risk mitigation strategies. This methodology follows the Pareto Principle and theorizes that 80 to 90% of the risk is contained in only 10-20% of the equipment.
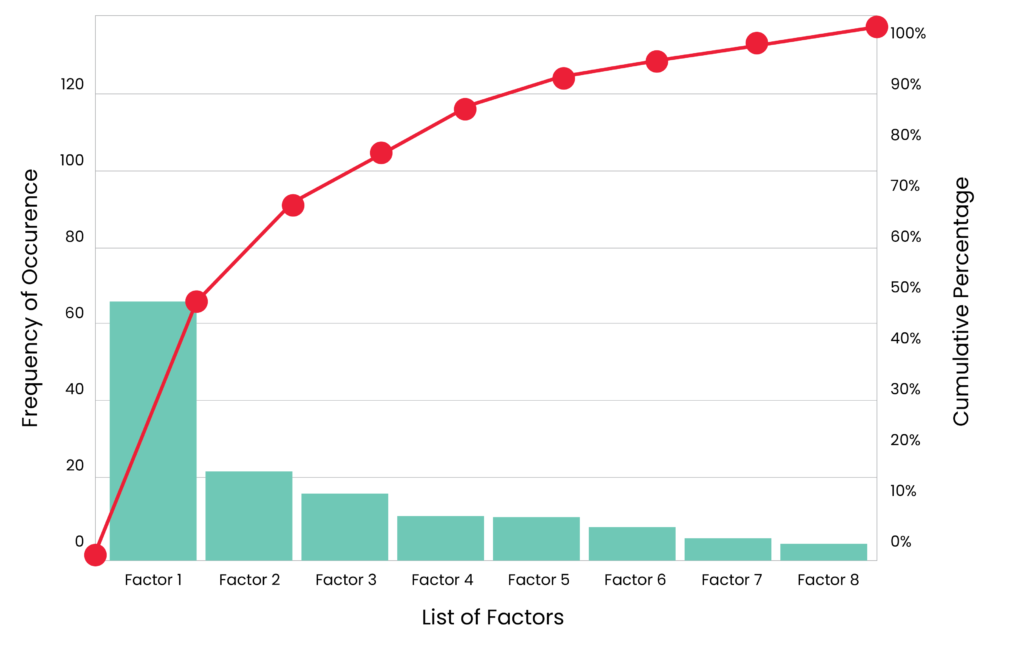
Conditions that drive risk are not always intuitive. A structured, consistent, and systematic process like RBI helps uncover issues that are not always evident. Sometimes the answer is inspection. Other times, the correct action might be the installation of a lining or cladding, and RBI may justify changing the materials of construction to achieve the desired level of risk or reliability. RBI, when implemented correctly, is a holistic process and requires looking at the equipment as part of a dynamic system.
Quality data is at the core of any RBI program, but how can those responsible for asset integrity easily and effectively manage this information? With thousands of assets to monitor, getting the data right and keeping it evergreened can be challenging. More often than not, knowing where to prioritize data clean-up and data collection efforts can make the difference between a sustainable or unsustainable RBI program.
Let’s look at Risk-Based Inspection, how it’s helped the industry, its limitations, and the future of reliability.
What Is Risk-Based Inspection?
Risk-Based Inspection (RBI) is an asset integrity management methodology that uses the probability of failure (POF) and consequence of failure (COF) to calculate risk for individual assets. The risk and risk drivers identified for each asset are then used to prioritize and drive inspection strategies that define where to focus inspection efforts, which methods are most effective, and when to perform inspections. RBI will also determine which action(s) is most appropriate to mitigate risk (e.g., inspection to increase confidence in the actual damage state of the equipment, repairs, replacement, lining installation, introducing a corrosion inhibitor). By targeting areas of high risk and performing prescribed inspections, complex process facilities can reduce unplanned failures, decrease the overall loss of containment risk, and increase the effectiveness of their inspection programs.
RBI is most prominently used in the downstream refining and chemical industries due to the high risk associated with their complex processes and operations. However, many industries—such as mining and wastewater—have adapted RBI to evolve their asset management programs. RBI, in many jurisdictions, will permit, when appropriate, on-stream inspections, which reduce risks and costs with entering a piece of equipment.
The American Petroleum Institute (API) guides risk-Based Inspection through recommended practices, API RP 580, Risk-Based Inspection, and API RP 581, Risk-Based Inspection Technology. API RP 580 details the minimum requirements and guidelines for implementing an effective RBI program, and API RP 581 provides recommended procedures and methodologies to be used in an RBI program.
An effective RBI program represents a key advancement toward meeting compliance with the U.S. Occupational Safety and Health Administration (OSHA) Process Safety Management (PSM) regulation. This regulation was created to ensure safety for facilities that contain hazardous chemicals. The rule requires process facilities with hazardous fluids to have documented plans addressing the assets containing these highly hazardous chemicals. Specifically, the PSM plans must help facilities understand, identify, manage, and reduce the risks associated with operating.
How Can Data-Driven Reliability Improve RBI?
A global mining and metals organization wanted to ensure its fixed equipment integrity program demonstrated compliance with industry codes, standards, and safe work practices. Pinnacle supported the organization with a Risk-Based Inspection pilot. The organization is now set up to have a successful Mechanical Integrity (MI) program, with projected savings of $7MM across an 11-year period.
A global mining and agriculture chemical leader needed to improve asset integrity and create consistency across sites after a loss of containment event. Asset integrity assessments were performed, and a Mechanical Integrity (MI) program implemented across 15 sites, leveraging Risk-Based Inspection (RBI) methodology.
Learn how we supported bp in creating an RBI and evergreening framework that created consistency across sites for safe, efficient, and cost effective operations.
A petrochemical facility was experiencing a high number of LOPC failures from its fixed assets and was looking for a cost-effective way to manage its assets. Pinnacle helped the facility to select and implement an IDMS, conduct RBI analysis, evergreen the program, and conduct inspections. Over the course of seven years, the facility reduced the number of LOPC failures by 62% and is now set up with plans and procedures for long-term success.
A refiner lacked a standardized inspection program and needed to proactively identify and mitigate its loss of containment (LOC) risks to meet compliance. Pinnacle implemented asset strategies for the operator’s piping across four sites which included appropriate considerations of the operations and maintenance practices of the piping. As a result, the refiner recognized 3X ROI and safely reduced the number of CMLs by 27.4%.
Why is Risk-Based Inspection Valuable?
Before RBI, oil and gas companies achieved asset integrity through a Time-Based Approach (TBA). A TBA can be inefficient because it often results in a large amount of resources being spent disproportionally on the risk of each asset. This practice also does little to encourage the operator to understand units, systems, loops, or the interdependent effects of operating practices on the equipment. A TBA is viewed as looking at equipment from an “after the fact,” or reactive perspective, and is often referred to as driving a car forward by looking in the rearview mirror. In contrast, RBI considers past, current, and future operating practices and their effect on the integrity of the equipment.
In the late 1990s, RBI was created to optimize this resource spend. RBI made a significant impact on the industry because it drove facilities to manage their Mechanical Integrity (MI) programs by risk, not time. RBI prioritizes inspections by risk and ensures resources are properly spent on the most troublesome assets at the correct times. Using risk as a guide, facilities operate more proactively, efficiently, and effectively.
The advantages of RBI include the following:
- Identification of risk drivers
- Development of an inspection plan focused on the damage mechanisms associated with the risk.
- Optimization and prioritization of inspection resources
- Identification of areas where process control monitoring can help manage and maintain risk in establishing proper Integrity Operating Windows (IOWs).
- Identification of mitigation activities that can further reduce the risk for the facilities and assessed equipment
- Acceptance and understanding of the current risk
- Provision for other applicable risk mitigation activities
- Risk impacts and projections for changes in process conditions such as opportunity crudes and de-bottlenecking.
- Continuous improvement in inspections execution and planning.
How does Pinnacle Conduct Risk-Based Inspection Differently?
Pinnacle has over 30 years of industry experience with numerous methodologies and applications for identifying the best solution. With not only a deep understanding of API 581 but other applications that help understand the sensitivities of the model to the data. Through Pinnacle’s Data-Driven Reliability framework, teams can help optimize any facility’s programs, no matter the program’s maturity, through data management, analysis, and contextualization. Our teams work hand and hand with customers and regulators to successfully identify appropriate risk programs and technology. Pinnacle can also help facilities in the following areas:
Program Implementation
- Defining the best solution through gap assessments
- Configuration of applications
- Risk training and establishing risk profiles
- Development of work processes and procedures
- Data collection and risk analysis
- Integration with CMMS/IDMS applications
- Execution of the risk-based plan
Program Sustainability and Continuous Improvement
- Advancing risk analysis through the use of AI technologies such as machine learning and natural language processing
- Staying up to date in regulatory requirements, codes and standards, and updates to the base technology
- Programs designed to work with other initiatives, such as IOWs, Management of Change, and reliability programs
- Evergreening support through Standard Operating Procedures (SOPs), training, MOC processing, Quality Management Plans (QMPs), and software support
Risk-Based Inspection Limitations
When it comes to managing inspections, an RBI program is a significant first step after a time-based program in the evolution of inspection program maturity. However, we need to look at the next evolution after RBI when it comes to further optimizing and improving system reliability performance. Specific limitations of RBI currently include the following:
- RBI models are typically very conservative due to core assumptions around generic failure frequencies, debits being applied for lack of data or information, and the calculation of POF and COF—particularly around health, safety, and environmental (HSE) risks. Additionally, over-conservatism often leads to dubious financial risk numbers where economic output is used. Once financial risk is used, most managers forget the results are based on relative instead of absolute risk (i.e., the dollar projections are relative).
- RBI only calculates the loss of containment risk (not functional failure) and helps drive inspection priorities accordingly.
- RBI calculations occur on an asset-by-asset basis and do not relate to the overall performance of the system, unit, or facility.
- RBI cannot be used to optimize an entire system, unit, or facility’s reliability strategy based on availability, cost, and resource constraints.
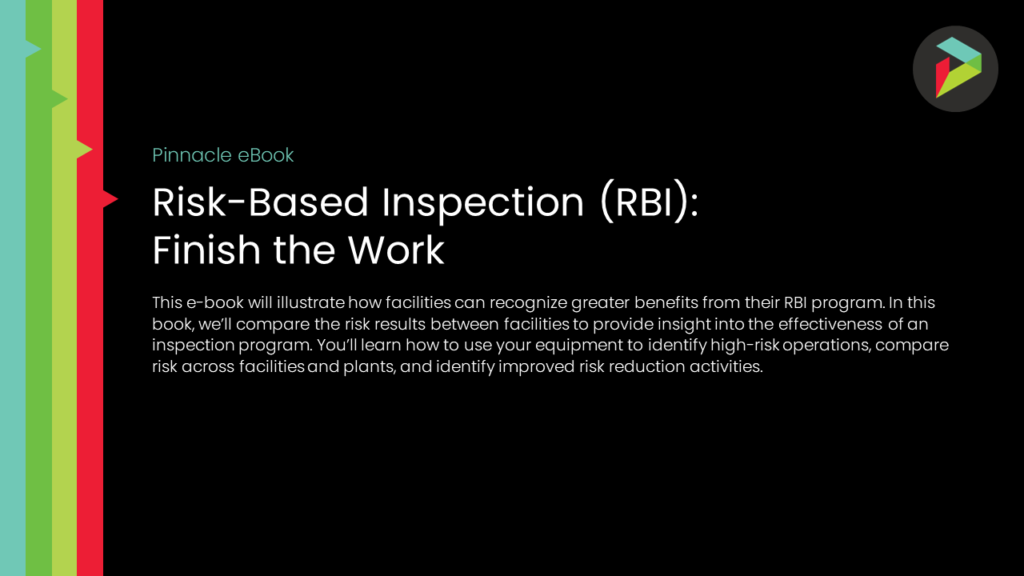
Featured eBook
What Does the Future of Reliability Data Look Like?
RBI, among other reliability methodologies, has helped the industry become more reliable, safer, and more cost-effective in deploying resources. However, the industry continues to see significant advancements in data acquisition, processing, warehousing, modeling, curation, and analytics. With these capabilities in hand, we can take the next leap in reliability analysis, allowing us to further improve reliability while optimizing total maintenance and inspection spend.
Quantitative Reliability Optimization (QRO) is an approach to reliability modeling which connects every relevant data point for all fixed and non-fixed assets at a facility to one integrated model, enabling enhanced decision-making for complex systems. In addition, QRO combines the power of traditional RBI models, subject matter expertise, and data science to provide a strong reliability analysis and even fill in the gaps where you may be missing data. QRO allows users to do things such as:
- Optimize all maintenance spend based on short/mid/long-term reliability targets
- Understand the economic value of every inspection or maintenance activity performed
- Scenario modeling, including the implications of moving a turnaround, changing feedstock pricing, or introducing various capital projects to the reliability of your facility.
- Understand the economic value of every piece of data currently being gathered or could be collected in the future
- Drive effective economic decisions in the event of reliability-based operating excursions.
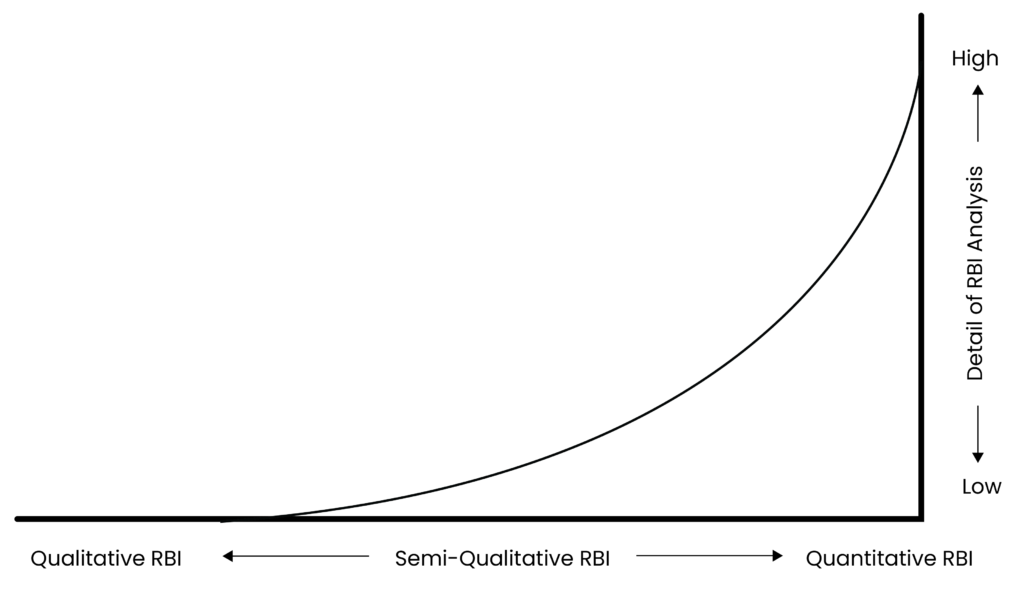
Stay in the know.
Providing data-driven insights, perspectives, and industrial inspiration from the forefront of the reliability transformation.