Unlocking Data-Driven Reliability for the Food & Beverage Manufacturing Industry
We help you use data to identify problems before they happen.
Use Data to Drive Reliability for Less
In the fast-paced world of food and beverage manufacturing, Pinnacle leverages the power of data to help you address challenges like unplanned downtime, waste reduction, and regulatory compliance. Our data-driven reliability framework seamlessly blends traditional reliability methods with cutting-edge data science and engineering. By doing so, we break down data silos, uncover hidden insights, and provide you with the actionable information you need to keep your facility running at its best.
Leveraging Technology With Human Expertise
While technology undoubtedly enhances operations, it cannot be relied upon as a standalone solution. A data-driven approach combines technology with human expertise, empowering your facility to make informed decisions.
Leveraging Data for Proactive Maintenance
Reactive maintenance is 3-5x more expensive than proactive maintenance. A proactive maintenance strategy, supported by data-driven insights, can optimize your maintenance activities, increase operational efficiency, and minimize costly unplanned downtime.
Maximizing Overall Equipment Effectiveness (OEE)
In the food and beverage industry, where strict regulations demand product quality, maximizing OEE is crucial. A data-driven approach maximizes your OEE by helping you maintain your equipment optimally, address potential failures, and implement quality control measures to ensure product quality.
We Help Industrial Leaders Navigate Reliability Digital Transformation
$20MM+
Invested in R&D and Ventures, focused on industrial reliability and data science
2MM+
Assets implemented and analyzed for reliability and integrity programs
500+
Employees dedicated to improving reliability, with 50% embedded in customer sites
20+
Reliability software packages implemented to enable data-driven decisions
Reliability as a Solution
Our fixed price service plus software solution focused on delivering to a quantified result. Back your reliability team with decades of experience.
- Improve reliability uptime by connecting data in single model.
- Dynamically prioritize maintenance and inspection activities.
- Transform culture through standardized processes and training.
$15.5M+
Increased annual revenue
6 Month
Timeline to improvement
Creating a Reliability Culture
Whether you’re in an operations, maintenance, or support function, every role has an impact on your facility. We help create a common, data-driven, framework of reliability that keeps you and your team on the same page.
Our aim is to assist you in prioritizing your time by pinpointing the assets that demand your distinct attention and suggesting the right techniques to employ to address the failure modes of concern.
Our objective is to provide you with a comprehensive overview of your facility’s performance in one glance. This is vital for making informed reliability decisions and mitigating unexpected shutdowns.
Our approach involves creating visible reporting views for all your facilities and collaborating to establish sustainable and scalable reliability work practices. Helping to prioritize resource allocation and minimize unplanned shutdowns, while boosting production.
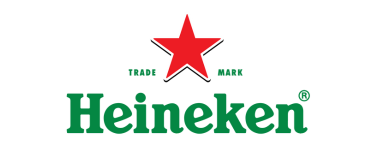
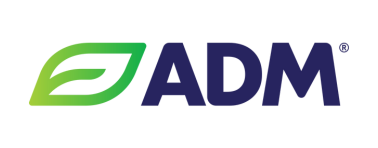
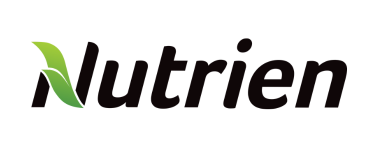
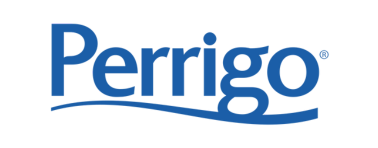
Increasing Profitability by $12MM Through a Risk-Based Reliability Improvement
Discover how Pinnacle’s risk-based reliability improvement process helped a U.S. manufacturing and packaging facility increase asset utilization potential by 20 percent, translating to an annual profit increase of over $12 million.
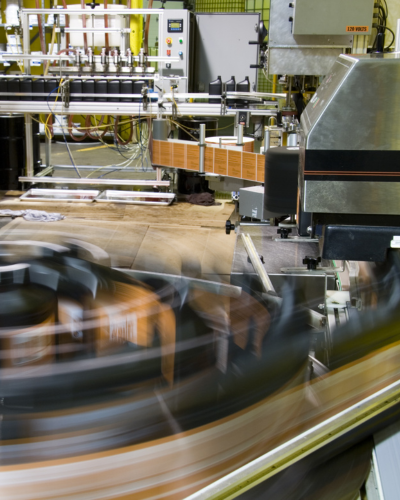
$12MM
Annual profit increase
20%
Asset utilization potential increase
Data Talks. Newton™ Listens.
The suite answering “What happens if this compressor blows?” or “Can I push this inspection?”. Single asset strategies are dated. It is time to take a system view of your availability, cumulative costs, and risk exposure for increased facility performance like you’ve never experienced.