What is Operational Readiness?
Operational Readiness (OR) is the development and implementation of operations, maintenance, and reliability (OMR) programs that occur during the Engineering, Procurement and Construction (EPC) phases of a project. These activities can start as early as the conceptual Pre-Front End Engineering Design (Pre-FEED) phase or at any time throughout the Front-End Engineering Design (FEED), Detailed Design, Commissioning and Start-up phases. The early implementation of these programs all contributes to the successful, cost effective and safe startup and ongoing operation of a facility.
Operational Readiness is a foundational data-driven model that solves many common problems that arise during greenfield and brownfield capital projects by integrating operational and maintenance aspects from conception to steady-state operations. Some additional benefits of Operational
- Operations and maintenance philosophies
- Reliability program development and implementation
- Mechanical integrity program development and implementation
- Data-driven risk modeling
- Operating and maintenance procedures
- Spare parts optimization
- Training
Why Implement Operational Readiness?
Today’s projects have become more complex and require an ever-increasing integration into multiple areas of customer operating organizations due to the large volumes of engineering and operational data that is required to effectively operate and maintain a facility over its expected design life. In addition, the challenges of both increasing government regulation and financial performance have significantly required owners to have all their operating systems and information in place prior to start up or the awarding of an operating license. To ensure no Loss of Primary Containment (LOPC) incidents and other challenges associated with start-up, operators must develop and incorporate extensive interrelated datasets and analytical models to have reliability from day one.
For example, a typical Master Asset List (MAL) can reach upwards of 90,000 asset tags, each with up to 20 associated attribute data items. When you consider that all these tags and associated data must be compiled, organized, validated, and uploaded into foundational Computerized Maintenance Management Systems (CMMS)/Inspection Data Management System (IDMS) systems prior to commissioning, it is easy to see not only the amount of effort it takes but also the level of expertise needed to ensure the data is correct and usable in a run and maintain environment. Coordinating this data from a multitude of cross-discipline sources, as well as vendors, is a significant task. That is also why it is important to incorporate design into the conversation with Reliability Centered Design (RCD). Operational Readiness and RCD go hand in hand when ensuring reliability success from the beginning.
When you also consider amassing the process and equipment information, development of risk models, operating and maintenance procedures, training, and spare parts, it is easy to see it is easier to perform these tasks during the EPC phases.
Why Implement Operational Readiness?
Today’s projects have become more complex and require an ever-increasing integration into multiple areas of customer operating organizations due to the large volumes of engineering and operational data that is required to effectively operate and maintain a facility over its expected design life. In addition, the challenges of both increasing government regulation and financial performance have significantly required owners to have all their operating systems and information in place prior to start up or the awarding of an operating license. To ensure no Loss of Primary Containment (LOPC) incidents and other challenges associated with start-up, operators must develop and incorporate extensive interrelated datasets and analytical models to have reliability from day one.
For example, a typical Master Asset List (MAL) can reach upwards of 90,000 asset tags, each with up to 20 associated attribute data items. When you consider that all these tags and associated data must be compiled, organized, validated, and uploaded into foundational Computerized Maintenance Management Systems (CMMS)/Inspection Data Management System (IDMS) systems prior to commissioning, it is easy to see not only the amount of effort it takes but also the level of expertise needed to ensure the data is correct and usable in a run and maintain environment. Coordinating this data from a multitude of cross-discipline sources, as well as vendors, is a significant task. That is also why it is important to incorporate design into the conversation with Reliability Centered Design (RCD). Operational Readiness and RCD go hand in hand when ensuring reliability success from the beginning.
When you also consider amassing the process and equipment information, development of risk models, operating and maintenance procedures, training, and spare parts, it is easy to see it is easier to perform these tasks during the EPC phases.
Case Study: Preparing for Recommission
Pinnacle worked with a North American operator to serve as a reliability partner during the recommissioning phase for one of their sites. The goals of the program were to achieve facility startup without a LOPC incident and maintain a minimum of 90% availability for a 5-year period before the first turnaround. Through expertise in reliability engineering, corrosion management, field inspection, data management, and project management, Pinnacle was able to tailor a resource and cost-efficient execution strategy to achieve the facility’s reliability and MI targets. The completed scope included:
- Reliability Availability Maintainability (RAM) simulation model
- Development of asset hierarchy
- Proactive and predictive maintenance strategies
- Inspection plans and baseline inspections
- Optimized spare parts program
- IDMS Implementation
- Development of critical repair procedures
- Corrosion modeling and asset strategies
The objective of Pinnacle’s Operational Readiness approach is to create sustainable philosophy and operating practices that result in a step-change improvement in the operations, maintenance, and reliability implementations of a facility. Operational Readiness is pivotal to all levels of an organization within a facility by focusing what is necessary to achieve the plant goals in the design phase.
The value of Operational Readiness to stakeholders include:
- Safer and smoother startup and transition to operation
- Mitigation of risks associated with scope, schedule, and communication misalignment
- Faster time to market
- Higher plant availability from startup
- Compliance with regulatory requirements
Operational Readiness is a pre-investment in your facility. The equivalent impact of performing ongoing annual maintenance tasks for your facility alone can range between 1-3% of the Total Incurred Cost (TIC) of the project. With the addition of annual operating costs, the total impact of maintenance and operations together can reach 4-5% of TIC. Considering that the facility will run for 30-40 years after it is built, this can be enough to cumulatively pay for the facility again.

How is Pinnacle’s Operational Readiness Program Implemented?
The Pinnacle Operational Readiness team works as an integration of your project team rather than as a separate scope. The Operational Readiness discipline specialists participate in design interfaces, reviews, reporting and other project activities using the same protocols as other disciplines in addition to executing their own technical scope. This scope includes developing philosophical approaches (Operations, Maintenance, MRO, etc.), OPEX and LCCA reviews, Reliability work (Master Equipment Lists, Master Asset Lists, Asset Hierarchies, Criticality Ranking, RCM, MI, RAM, FMEA, etc.), Maintenance Strategy development and authoring of Maintenance and Operating Procedures. Being software agnostic, Pinnacle has in-depth experience implementing numerous software types and can assist in populating and/or implementing CMMS, IDMS, and spare parts catalogs.
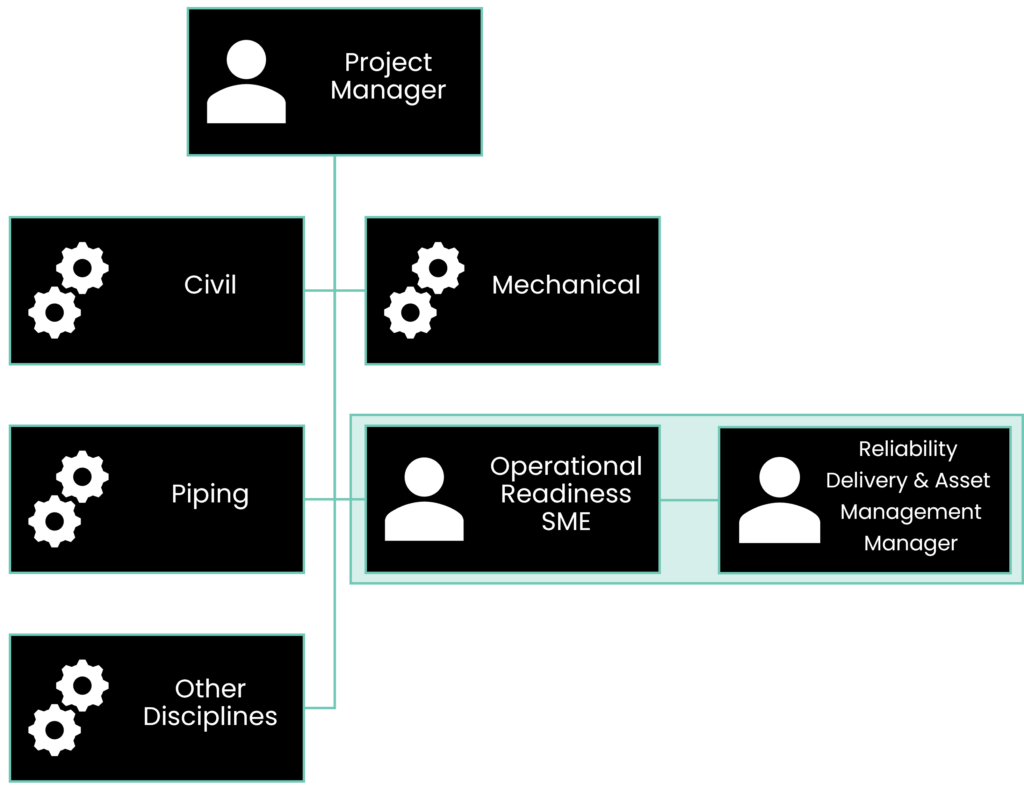
Once your facility is up and running it is important to continue to evolve your reliability programs to maintain safe operations and maximize availability. Learn more about the next evolution of data management and modeling with Data-Driven Reliability.
Stay in the know.
Providing data-driven insights, perspectives, and industrial inspiration from the forefront of the reliability transformation.