What Is a Process Hazard Analysis?
A Process Hazard Analysis (PHA) is a systematic method of identifying hazards associated with handling hazardous chemicals and developing a list of recommended actions to minimize associated risks.
Processes meeting the highly hazardous chemicals threshold requirements in the United States are required to perform PHAs per the Occupational Health and Safety Administration’s (OSHA) Process Safety Management (PSM) standard and the Environmental Protection Agency’s (EPA) Risk Management Plan (RMP) Rule.
How Can Data-Driven Reliability Improve PHAs?
Data-driven reliability is the framework for reliability improvement that connects results from your PHAs to your business decisions. This approach employs reliability intelligence and incorporates conventional models and expertise from Subject Matter Experts (SMEs) to provide facilities with the insights needed to achieve sustainable operations. This framework is based on the fact that the key to success is not gathering copious amounts of data but obtaining relevant, high-quality data that powers the models.
How Is a Process Hazard Analysis Conducted?
A PHA is conducted by a cross-functional team, including engineering, operations, maintenance, and safety experts, who can effectively identify hazards and recommend specific actions to control the potential hazards and minimize the risk of failure.
Several methods can be used to perform a PHA, including “what-if” analyses, checklist methods, hazard and operability studies (HAZOP), Failure Modes and Effects Analyses (FMEA), and fault-tree analyses. Despite differences in the various methodologies, the PHA team determines the feasibility of specific failure scenarios, evaluates the consequence of the scenario, and makes recommendations as necessary to reduce the overall risk of the system under review. According to the OSHA standard, PHAs should be updated at least every five years. An effective Management of Change (MOC) process can also make the PHA update much more manageable.
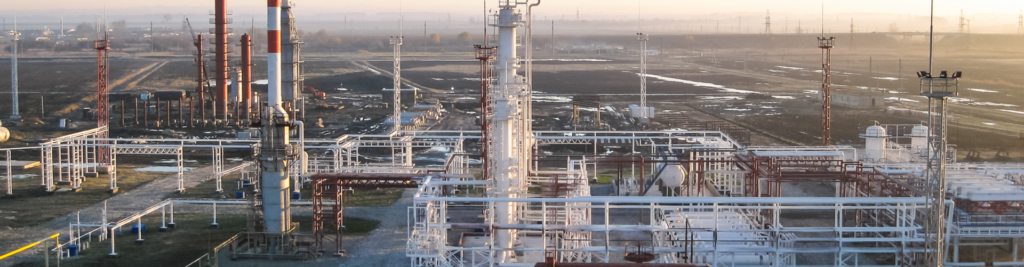
What Is the Next Evolution of Reliability Analysis?
PHAs are essential tools for identifying hazards and risk mitigation plans. However, we know completing a PHA can be a time-consuming and resource-intensive process.
PHA updates are conducted on a reoccurring cycle and typically done around the same time as other analyses, such as Layers of Protection Analysis (LOPA), Risk-Based Inspection (RBI), Life-Cycle Cost Analysis, Reliability Centered Maintenance (RCM), critical spares, and RAM modeling. The “O” in HAZOP stands for operability and is intentionally focused on safety consequences
With major advancements in data acquisition, warehousing, modeling, and analytics, we can take the next leap in reliability analysis and improve upon the PHA process. This leap is possible through Quantitative Reliability Optimization (QRO). QRO is a reliability modeling approach connecting relevant reliability data points at a complex facility into one integrated model, allowing for near real-time complex decision-making. QRO enables facilities to create a holistic program by combining these analyses for improved decision-making capabilities.
QRO empowers you to enhance your PHA process with the following:
- Quantify the likelihood and consequence of failure using near real-time asset data
- Provide insights into facility-wide impacts of failures
- Quantify the effect of the recommended changes by PHAs
- Accommodate any PHA methodology
Stay in the know.
Providing data-driven insights, perspectives, and industrial inspiration from the forefront of the reliability transformation.