Introduction to Root Cause Analysis
Nothing fails without a cause or reason. When something does go wrong at your facility, it’s important to identify the true reason or cause of the problem. A Root Cause Analysis (RCA) investigates why issues happen, leading to changes in procedures, processes, or design that can prevent similar failures from occurring in the future. Fewer failures mean improved safety and reliability.
What Is a Root Cause Analysis?
Root Cause Analysis (RCA) is a methodical process of identifying the root cause(s) of a problem. Root cause analysis allows facilities to prevent future instances of failure by identifying the causal factors that contributed to the event with safety, health, environmental, reliability or production impacts, rather than simply correcting the proximate or immediate cause of the failure. By investigating how and why a problem occurs, changes can be made to procedures, processes, or design that will prevent similar failures from occurring.
The RCA process utilizes a wide variety of analytical and statistical techniques to initiate an analysis, perform an analysis, and implement solutions. Solutions derived from the RCA process should meet the following expectations:
- Prevent the problem from recurring, or at least maximize the interval between reoccurrences of failure considered to be acceptable or unavoidable
- Be justifiable in regard to risk, cost and/or policy
- Mitigate the consequences of failure
- Be properly integrative throughout associated areas and not create new problems
- Meet the goals and objectives of the organization
- Be within the control of the people implementing the solution(s)
Once the solutions are identified and implemented, it is important that they are monitored and validated as effective. An RCA can be considered successful when it identifies elements that, when removed from the timeline, prevent the failure from occurring or significantly reduce the impact of the failure. However, an RCA can fail for a few reasons.
Why a Root Cause Analysis Can Fail
The success of an RCA is negatively impacted by a reliance on assumptions, missing information, and failure to implement corrective actions.
Reliance on Assumptions
One of the most common reasons that RCA fails is the rush to judgement. The RCA team relies on assumptions about the likely root cause and seeks confirmation for their assumptions rather than allowing the facts to speak for themselves. This is one reason why it is important to have an experienced facilitator lead the RCA process.
Missing Information
Other issues with RCA include poor team composition, without all relevant personnel or experts available to provide input. If the root cause is a problem with process logic, and the automation team or SCADA programmer is not present, the analysis may veer off course and focus on personnel, materials, or management issues that are secondary to the root cause. Lack of communication or available resources can further derail an RCA, as missing information will not be included in the analysis. Missing information can result in poor solutions that do not address the true root cause.
Failure to Implement Corrective Actions
Oftentimes, the corrective actions developed at the end of an RCA don’t get implemented and there is no accountability as to whether this happens. This may be an indication of insufficient management support of the RCA effort.
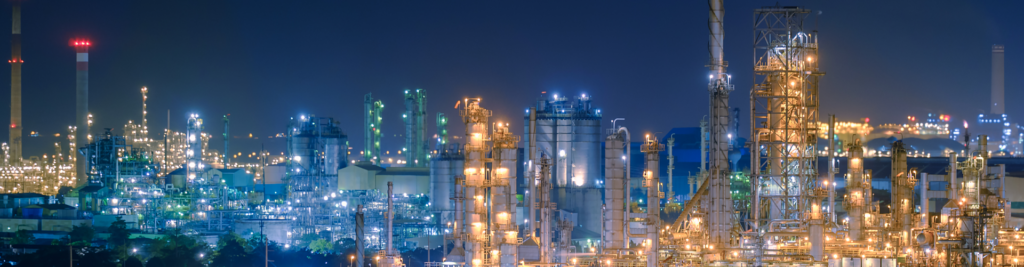
Enhance Your RCAs with Data-Driven Reliability
RCAs are important for identifying root causes of failure so that similar failures can be prevented in the future. To receive the full value of an RCA, we need to ensure they are successful. With major advancements in data acquisition, warehousing, modeling, and analytics, we have the opportunity to take the next leap in reliability analysis and ensure RCAs are successfully performed.
We believe this leap is being made possible through Quantitative Reliability Optimization (QRO). QRO is an approach to reliability modeling which connects every relevant reliability data point at a complex facility to one integrated model, allowing for near real time complex decision making that allows users to do things such as:
- Near real-time optimization of all maintenance spend based on short/mid/long term reliability targets.
- Understand the economic value of every inspection or maintenance activity performed.
- Understand the economic value of every piece of data that is currently being gathered or could possibly be gathered in the future.
- Near real-time scenario modeling, including the implications of moving a turnaround, feedstock pricing changes, or various capital projects.
- Drive effective economic decisions in the event of reliability based operating excursions.
A key driver for the successful outcome of an RCA event is the implementation of the corrective actions. However, it’s not only just about implementing a series of actions, it’s implementing the actions that have the true impact to rectify the causes that contributed to the event. With QRO, data that is attributable to the event and the mitigating actions can be analyzed to determine the impact they have on the preventing a future event.
Another key finding from RCA events is not only identifying the causal factors that were attributed to the single event, but also the ability to see repetitive causes across multiple events. By letting you see the impact that each data point has on your facility, QRO lets you get more out of your RCA events by enhancing your insight and analysis into commonality of cause.
Learn more about Quantitative Reliability Optimization.
Stay in the know.
Providing data-driven insights, perspectives, and industrial inspiration from the forefront of the reliability transformation.