What Is Reliability Simulation and Performance Optimization?
Historically, it has been difficult to quantitatively determine how actions affect facility performance. With Quantitative Reliability Optimization (QRO), you can leverage causal links established with the Asset Reliability Analysis (ARA), Lifetime Variability Curves (LVC), and a system model to allocate resources to achieve strategic reliability targets optimally.
The last element of QRO is reliability simulation and performance optimization. This element builds off the previous three elements and helps facility leaders see what actions they need to take to prevent asset failure, along with the time these actions should be taken.
How Does Reliability Simulation and Performance Optimization Work?
Taking the conclusions from the ARA to see the effects one asset has on the system paired with the LVC outcomes, reliability simulation, and performance optimization gives facility leaders insight into how each action impacts reliability, performance, and availability – all at the system level. These insights allow leaders to move away from individual tasks for individual assets and truly focus on the high-level reliability of their systems and, ultimately, goal seek reliability. With QRO, you can create more proactive reliability plans using the data you are already collecting and make more reliable decisions.
Below is a sub-section of a reformer for an independent refiner with about 80 assets – a blend of fixed equipment, rotating assets, and I&E assets. This facility has best-in-class Risk-Based Inspection (RBI), Reliability Centered Maintenance (RCM), and spare parts programs. It has a 10-year projected 96% availability and 10-year planned spend of $1.33 MM to maintain availability and manage HSE risk. This scenario prompted the question, “How can we boost availability while maintaining the budget?”
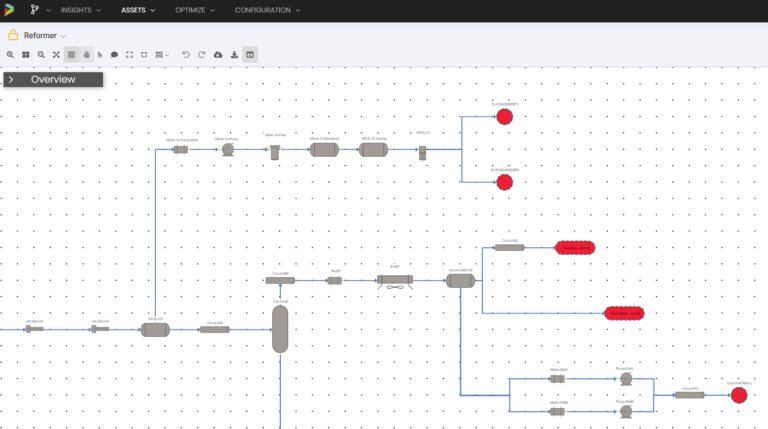
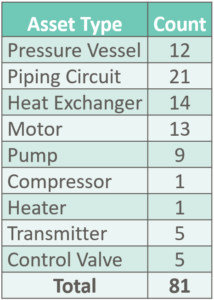
Leveraging QRO principles, the refiner was able to identify areas where tasks didn’t add value, areas where the most appropriate data was not being collected, and areas where there was wasted spend. Through QRO, this facility was able to recognize the following:
- Reduction in overall fixed equipment inspection spend
- Extension of PM intervals
- Increase in availability by 3%
- Reduction in spend by $50,000
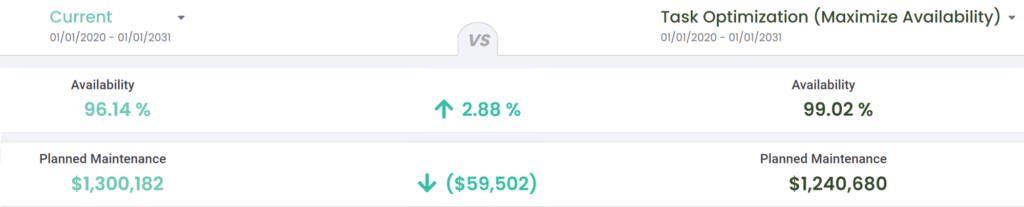
Benefits of Reliability Simulation and Performance Optimization
As in the example above, facilities can recognize many benefits by implementing reliability simulation and performance, including:
- Understanding how every action impact performance, gaining efficiency in data analysis, and modeling any scenario to understand how each input affects facility output
- Ensuring plans are in place to achieve targets, driving measurable improvement in availability, and seeing a holistic view across all assets without silos
- Enabling integrated reliability, identifying lost value in spend to ensure the highest return on capital, and connecting short-term actions to long-term strategies
Stay in the know.
Providing data-driven insights, perspectives, and industrial inspiration from the forefront of the reliability transformation.