Learn how we helped a North American– based energy company better manage their risk and improve safety and inspection spend through a CML Optimization pilot.
Challenge
A North America-based company needed a solution to better manage risk associated with operating certain equipment.
Solution
Rooted in traditional CML Optimization, Pinnacle developed a data-driven CML Prioritization program.
Result
As a result, the company can now prioritize inspection activities, increasing safety and reducing inspection costs.
Introduction
A refinery in North America experiences varying amounts of corrosion in certain areas of piping across three different units. Due to the high corrosion in parts of some units, these stretches of piping are replaced at their respective three or four-year turnaround cycles, and as a result, the thinning data being captured has a short effective period with which to do predictive modeling. To reduce the risk of corrosion and optimize inspection costs, the company operating the refinery initiated a process improvement initiative. As part of this initiative, multiple approaches were considered to pilot different methodologies to improve the effectiveness of the data collected, overall reliability, and mitigate risks associated with equipment failure. Among those, they selected Pinnacle’s process to prioritize condition monitoring locations (CMLs) and frequencies using data science coupled with corrosion/materials & inspection engineering to better identify areas of vulnerability, characterize degradation attributes, ensure the right CMLs are inspected at the right time, and reduce inspection spend on ineffective CMLs.
CMLs have long served to be at the whim of linear approximations of previous thinning history, with little emphasis on projecting past CML performance from historical data onto piping being replaced and the new CML, industry experience specific to the service, or a valid corrosion or damage mechanisms review. CML Prioritization by the methodology presented in this case study is a new CML Optimization methodology and predicts future thinning based on past performance from that same CML across repairs and replacements, ranking CMLs by the risk posed to safety and production prior to the next scheduled action (repair/replacement/inspection/turnaround) taken on that CML.
The Challenge
The company had an overarching goal to reduce and better manage operating risk across all sites and implemented a multiyear initiative to analyze the piping circuits and pressure vessels using risk-based inspection analysis and corrosion monitoring with commensurate inspection interval processes. As a result, they identified that these processes were unique to each site, and they embarked on a standardization campaign that spanned to align these practices and pilot potential improvements. As a part of an experimental venture, this specific site was chosen to pilot a data-driven intelligence model that would help prioritize and optimize CML locations. The goals of this project were to:
- Better manage risks associated with operating the equipment
- Identify areas of vulnerability and recommend changes to CMLs and other practices to improve reliability
- Reduce wasted CML activities as appropriate that add no value to the health monitoring of the asset
- Identify optimal required coverage to safely continue operations while maintaining confidence in measuring facility integrity
- Increase confidence in the program by identifying bad actors and quantifying their level of uncertainty and additional data clean up needs
- Provide proof of concept of CML Prioritization to identify overall value to the business
- Produce data-driven end-of-life calculations for piping circuits
Pinnacle's Solution
The purpose behind inspection is to assess the integrity of a facility’s assets, quantify risk, and predict degradation rates to better manage reliability. In an ideal world, a facility would complete full inspections for all of its assets at every opportunity. However, this type of approach to inspection is unrealistic because of constraints in manpower, inspection budgets, and time. For this facility, Pinnacle presented a practical alternative to evaluating CMLs, in a way that would enable the facility to conduct inspections proportionally to risk. Traditional CML optimization methods are focused on determining the minimum amount of CMLs that should be assigned to an asset to confidently monitor active damage mechanisms and corrosion rates. These programs are typically concerned with eliminating CMLs by analyzing inspection scope, techniques, and intervals that can cause unexpected failure events and compares them to the types of degradation expected, to make qualitative decisions about reducing CMLs.
Pinnacle leveraged an intelligence model rooted in data science and enhanced by traditional CML Optimization methodology. This also creates a model that can be dynamically updated to maximize reliability and return on investment (ROI) as the latest information becomes available. Being able to apply the new data adjusts and improves the model with each iteration. As a part of this method, a Lifetime Variability Curve (LVC) is created for every CML and projects into the future the probability distribution for that CML thickness across a range of dates. LVCs’ inputs include historical inspection data, asset data trends, subject matter expert knowledge, and modeled corrosion rates based on process and operating conditions and maintenance histories to determine a probability of failure for a given failure mode. Unlike traditional methods, CML Prioritization takes degradation rates and uncertainty of the facility’s data into account which impact the accuracy of predictions.
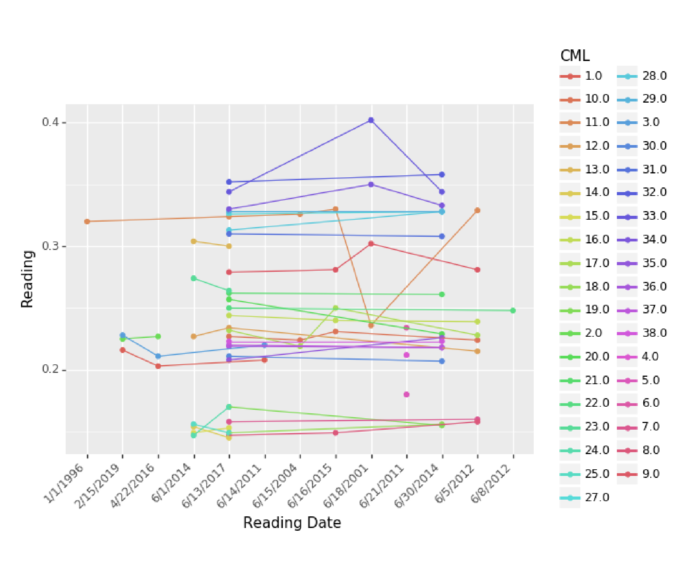
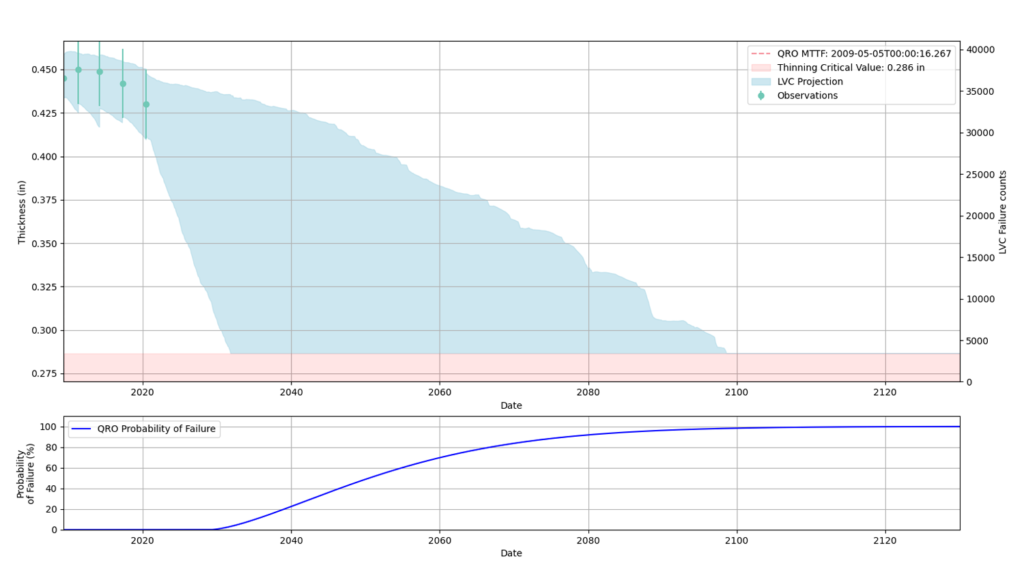
Using these types of analyses, we can assess the value of inspecting each CML, focusing more on prioritizing existing CMLs and using the LVCs to determine the CMLs that will need updated measurements or assets that need replacement within a specified window of time. This approach assumes that the CMLs in existence are sufficient to accurately determine the degradation state of each asset (which was a valid assumption in this case, given the extensive CML coverage of the assets involved in the study). Some CMLs may provide little value in the next inspection and would not be recommended to be taken until a later date when the expected thickness is below a predetermined threshold or at too high an uncertainty. At this stage, two diverging approaches are available to adjust inspection cost: Integrity Confidence or Event-Based Prioritization.
In the Integrity Confidence approach, the LVCs are used to determine the minimum required CMLs on each asset to reach a 95% confidence in measuring the thinning threats to that asset, ensuring that when a threat to primary containment occurs, there’s a 95% chance that one of the selected CMLs will measure that threat. Through this analysis, it has been discovered that some CMLs are more valuable than others when it comes to individual inspection events. In the example below only seven CMLs are required to reach that 95% confidence threshold out of a total of 27 CMLs on that asset, resulting in a potential reduction of inspection activities for 74% CMLs.
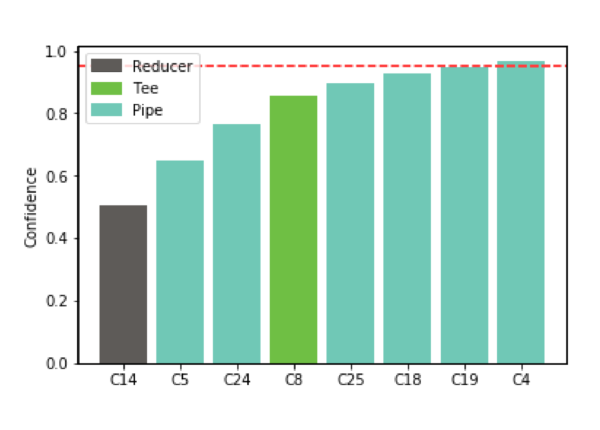
The Event-Based Prioritization approach used the LVCs to identify all CMLs that measure a thinning integrity threat to their respective assets by a specified date. In this study, the date was set as the second next turnaround of each unit, so that if the thinning threat measured by a CML would cause a loss of primary containment, it could be replaced or repaired in the closer turnaround event. Additionally, this approach identified CMLs that indicated asset failure within the next one to two years, prior to the next inspection event, and required immediate attention by the facility. The emphasis in this approach is on timing; all CMLs will eventually measure integrity threats if the asset isn’t repaired or replaced, but only certain CMLs need to be inspected to evaluate if an integrity threat is likely to occur before scheduled maintenance happens.
Both approaches benefit from the grouping of CMLs into CML Families or sets of CMLs that experience similar corrosion parameters (i.e., temperature, sulfur-content, and other damage-mechanism-specific factors) and physical characteristics (i.e., component type, component orientation, proximity to specific assets). These CML Families allow for thinning history to be shared across its members, taking the place of modeled corrosion rates in determining the initial rate for each CML.
Results
In partnership with the Pinnacle data science team and Mechanical Integrity (MI) subject matter experts, the facility met its goal of identifying the inspection events required to mitigate risk in the most cost-effective manner possible and to maximize the value of spend in their MI program. The estimated business impact to the facility resulting from the optimization analysis and resulting prioritization scheme is minimally $384,000 in reduced inspection spend over the next two turnaround cycles. The savings are due to postponement of non-value-adding inspection activities and inspection scope, resulting from the reduction in recommended CML monitoring as well as a decrease in inspection frequency. The project results included:
- Improved monitoring capabilities and reduced risk on analyzed circuits
- Recommendations to improve monitoring of high risk/high value components within the circuits
- Provided proof of concept of statistical CML Prioritization to maximize the value of inspection spend to the business
- Potential savings of $384K to $768K for six piping circuits across a 10-year period by reducing spend on unnecessary inspections
- Creation of CML Prioritization categories (Critical, High, Low), which were then mapped to each CML and guided inspection scheduling
- Increased plant safety with the reduction of manpower in the field as a result of reduced inspection activities
Conclusion
CML Prioritization empowered the facility to take action in planning their inspection spend to focus on the most critical areas of these circuits. Prioritization means putting focus on inspecting CMLs in proportion to the risk that they pose to ongoing production within a facility, while not neglecting to gather inspection data for CMLs that will one day become high priority as they reach end of life. In addition to the prioritization, Pinnacle was able to provide upgrade recommendations to further improve the impact of these results and the facility is exploring scaling this methodology to the rest of the site.
Stay in the know.
Providing data-driven insights, perspectives, and industrial inspiration from the forefront of the reliability transformation.