Introduction to Reliability Centered Design
When building a new unit or facility, asset reliability is often not considered as part of the design. However, inefficient design can result in high life cycle cost over an asset’s operational life. That’s why it’s important to ensure you’re planning for reliability as early as the front end engineering and design (FEED) phase, as it’s the most cost-effective way of making a facility reliable to maximize production and return on investment.
Reliability Centered Design (RCD) is a popular analysis used to build asset management principles into the design of a greenfield facility or capital project. While RCD does provide efficiencies surrounding maintenance and life cycle cost, it does not provide detailed insight into the impact of design changes on system availability. It also leaves room for more finely tuned data to enhance the analysis results, which leads us to what we believe is the next evolution in reliability data modeling: Quantitative Reliability Optimization (QRO).
Let’s dive into how designing for reliability has evolved with RCD and how it will continue to evolve with QRO.
What Is Reliability Centered Design?
Reliability Centered Design (RCD) analysis builds asset management principles into greenfield facilities during the FEED stage of a project by identifying key contributors to system unavailability and recommending design changes to improve system availability without sacrificing its operational goals.
RCD employs Reliability Centered Maintenance (RCM) methodologies—specifically, Failure Modes and Effects Analysis (FMEA)—to incorporate reliability principles into the design, which will enhance equipment reliability, system availability, and asset maintainability. RCD’s goal is to maximize the reliability of the system, reduce total life cycle costs, and streamline equipment and designs to reduce operation and maintenance costs.
Reliability Centered Design Process
The RCD process includes a complete review of the design from the perspective of key operations and maintenance staff, management, and process experts. Design deficiencies that affect system reliability and availability are identified and risk-justified redesign recommendations are provided for review and possible incorporation into the project design. The RCD process also identifies equipment configuration best practice opportunities and critical/capital spare parts. RCD then forms the foundation of a reliability-based asset management program through expansion into full RCM for the final design.
History of Reliability Centered Design and Reliability Centered Maintenance
RCD is based on Reliability Centered Maintenance (RCM), a maintenance strategy developed by the airline industry in the 1960s.
Before RCM, asset intensive industries relied on time-based maintenance to keep assets in good operating condition. A time-based approach was highly inefficient because it required a large number of resources (and hence, high spending) to maintain the maintenance program. It also did not provide a significant impact on improving an asset’s reliability.
RCM transformed the way asset intensive industries performed maintenance because it meant a maintenance program could be driven by risk, rather than time. Gaining the ability to prioritize risk and appropriate risk-mitigation tasks, oil and gas companies were able to create much more efficient maintenance strategies.
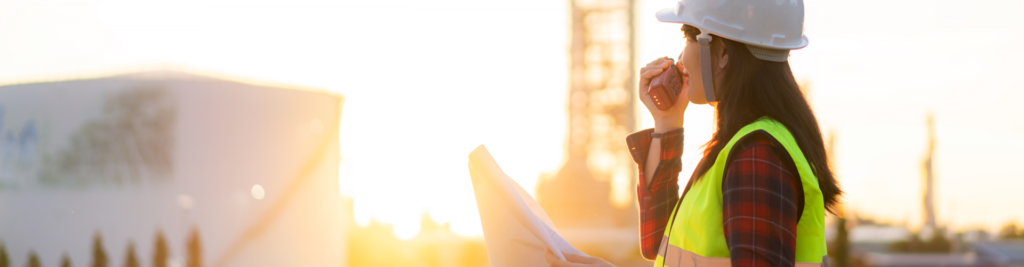
Quantitative Reliability Optimization (QRO): The Next Evolution of Reliability Data
RCD and RCM have helped the industry achieve greater levels of safety and reliability while also helping to generate more cost-effective strategies. However, advancements in data acquisition, modeling, warehousing, and analytics are now providing the next evolution in reliability—one in which reliability can be further improved and maintenance and inspection spend can be further reduced. We believe this leap is being made possible through Quantitative Reliability Optimization (QRO). QRO is an approach to reliability modeling which connects every relevant reliability data point at a complex facility to one integrated model, allowing for near real-time complex decision making that allows users to do things like:
- See how a facility will perform in the future and understand where to focus maintenance efforts.
- Near real-time optimization of all maintenance spend based on short/mid/long-term reliability targets.
- Understand the economic value of every inspection or maintenance activity performed.
- Understand the economic value of every piece of data that is currently being gathered or possibly gathered in the future.
- Near real-time scenario modeling, including the implications of moving a turnaround, feedstock pricing changes, or various capital projects.
- Drive effective economic decisions in the event of reliability based operating excursions.
Learn more about the next evolution of data modeling, Quantitative Reliability Optimization (QRO).
Stay in the know.
Providing data-driven insights, perspectives, and industrial inspiration from the forefront of the reliability transformation.