What is Reliability Digital Transformation?
Digital transformation refers to the acceleration of an existing process through digital conversion, resulting in faster data collection, analysis, and decision making. Digital transformation started to become a major focus of heavy asset industries during the ramp up of software in the 1990s when these industries began digitizing their documentation. This digitization process forced facilities in these industries to manage different data sets digitally instead of just on paper, improving the models that focused on the processes, real-time operational alerts, and types of maintenance and inspection tasks that should be performed at these facilities.
Today, industrial leaders are actively working on digital transformation initiatives, focusing on properly leveraging their data to enable more sustainable and profitable operations. One key part of a successful transformation is reliability and maintenance. We call this Reliability Digital Transformation.
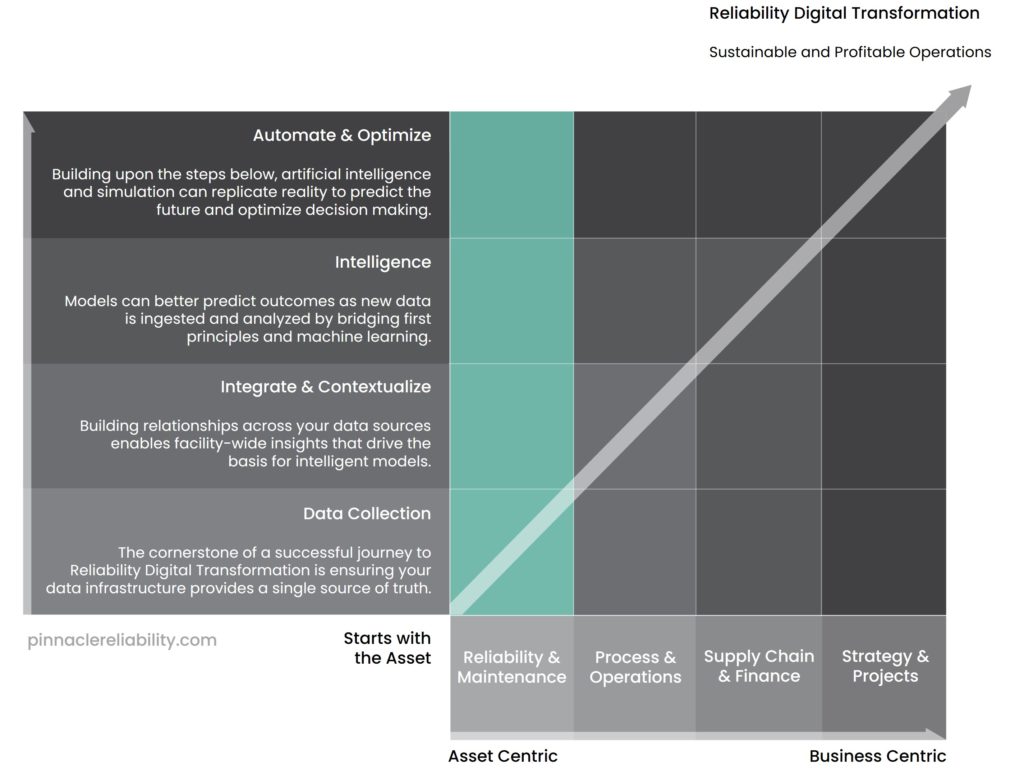
Without the focus on reliability and maintenance, true digital transformation will not be realized. Why? Because industrial facilities are in the business of production and in order to be successful, their assets must perform and operate reliability.
If done correctly, reliability digital transformation will help industrial facilities make better, faster decisions with fewer labor hours and less material, reducing overall maintenance spend, decreasing safety risk, and increasing profitability and sustainability in operations.
Reliability is Sustainability
A key piece to sustainable operations often not associated with digital transformation is a strong reliability and maintenance strategy. Reducing waste and driving long-term profitable operations is more important now than ever before. As a result, many industrial facilities have a renewed focus on incorporating sustainability practices into their programs by changing their asset makeup through either divestiture or acquisition, or by focusing on the optimization of their existing assets through digital transformation initiatives.
The most reliable operators are also the most sustainable operators.
Through our analysis of the economic impact of reliability in the refining, water and wastewater, and mining industries in our Economics of Reliability Reports, we found that the most sustainable operators lead the industry in minimized unplanned downtime and mitigated process safety risk. Additionally, these leaders ensure their reliability and maintenance funds are effectively spent.
How can industrial facilities become more sustainable through reliability? By integrating a successful reliability strategy into their processes. Driving a successful reliability strategy requires reliability digital transformation across the data supply chain, ranging from what data is gathered to how it’s organized, contextualized, and analyzed to drive decisions. This process is called data-driven reliability.
Data-Driven Reliability
Data-driven reliability is our approach to reliability-based digital transformation and requires transformation across the entire reliability data supply chain. Data-driven reliability is comprised of four primary steps: data, integrate & contextualize, intelligence, and automate & optimize.
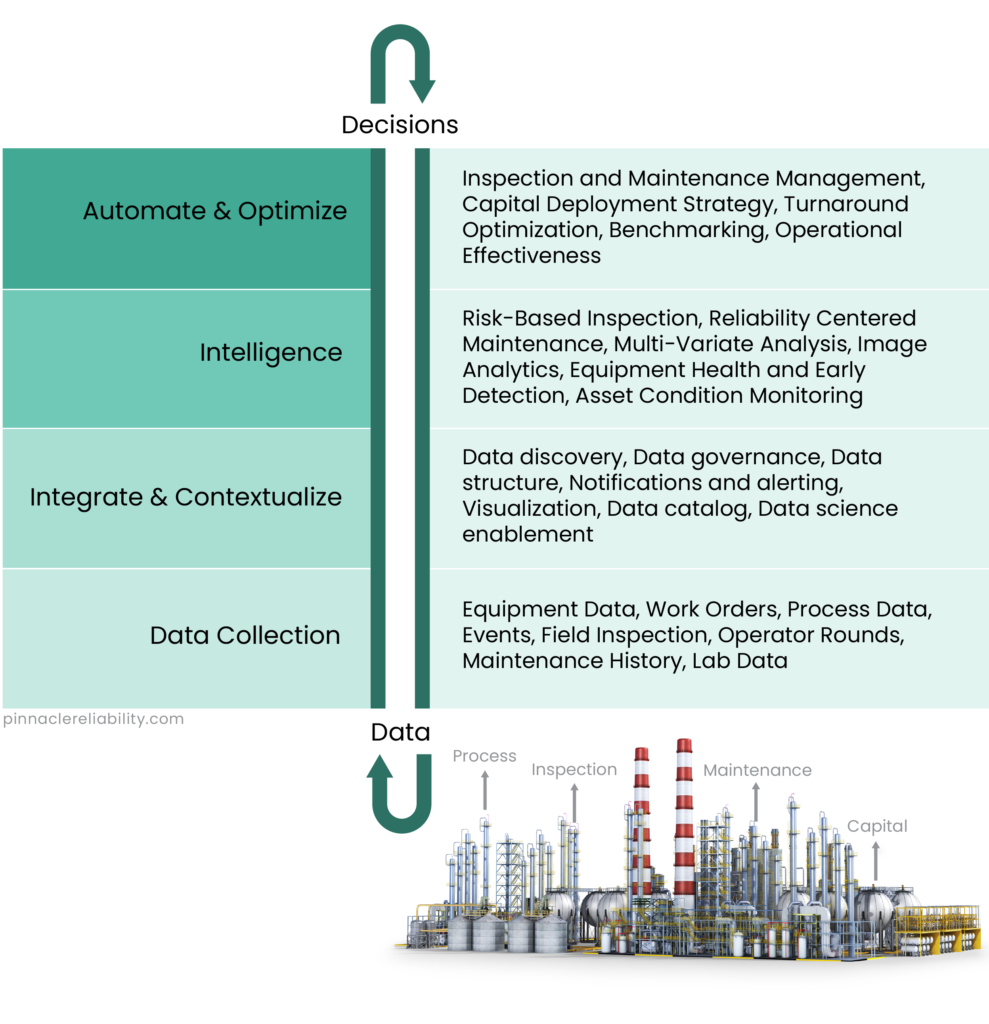
Data collection:
The first step focuses on the collection and storage of all data collected at facilities today such as process data, visual or non-destructive examination inspection data, maintenance data, and capital and operational expenditures. The cornerstone of a successful reliability digital transformation is ensuring your data infrastructure provides a single source of truth. Even if you don’t have confidence in your facility’s data today, a fundamental understanding and alignment across your organization on your data strategy is critical to long-term success.
Integrate and contextualize:
The second step focuses on the organization and contextualization of the data structure. During this step, facilities focus on building relationships across their data sources to ensure they’re bringing data together in the right ways. Many facilities currently have untapped data and overlapping systems, making it more difficult to access data and know which data adds value to their facility.
Intelligence:
The third step focuses on the models and intelligence that are being fed by the data organized during the previous two steps. Today, there are a variety of different types of models that focus on different asset types, failure modes, time horizons, and applications. These intelligence layers are typically split between engineering models and data science models, making complex decisions across asset types, failure modes and time horizons difficult to make. Data-driven reliability brings these complex models together to empower more effective and efficient decision making.
Automate and optimize:
The fourth step focuses on ensuring intelligent insights can be properly applied to the process and operational strategy, capital deployment, preventative and predictive maintenance execution, and turnaround planning.
Data-driven reliability is an essential pillar for industrial digital transformation, helping owner/operators leverage their data for sustainable and profitable assets.
How We Deliver Value
Data-Driven Assessment:
Every engagement begins with a data-driven assessment that identifies opportunities for a facility to reduce unplanned downtime, optimize maintenance and inspection spend, and mitigate process and safety risks. Our assessment includes a quantified road map that considers every element of a reliability digital transformation journey across your facilities’ people, process, and technology and quickly delivers value.
Targeted Improvement
Leveraging our horsepower, reliability engineering expertise, and data science, we provide a holistic delivery model that brings together the best in project management, service, technology solutions, and training. Prior to any project kickoff, a quantified value proposition is agreed upon and then measured upon completion. It is through this approach that we ensure that every solution is driving impact and minimal time is wasted.
Sustained Improvement
Our team ensures that every improvement is evergreened and connected to your business decision cadence. We constantly optimize and adjust our road map to ensure that we are maximizing performance at the lowest cost possible while maintaining safety.
Stay in the know.
Providing data-driven insights, perspectives, and industrial inspiration from the forefront of the reliability transformation.