Let Data Drive
Your Reliability
Data-Driven Reliability is the lens we use to view the impact of data across an organization’s people, processes, and technology. This framework for performance improvement ensures your data fuels the right models to help you make more confident, strategic decisions.
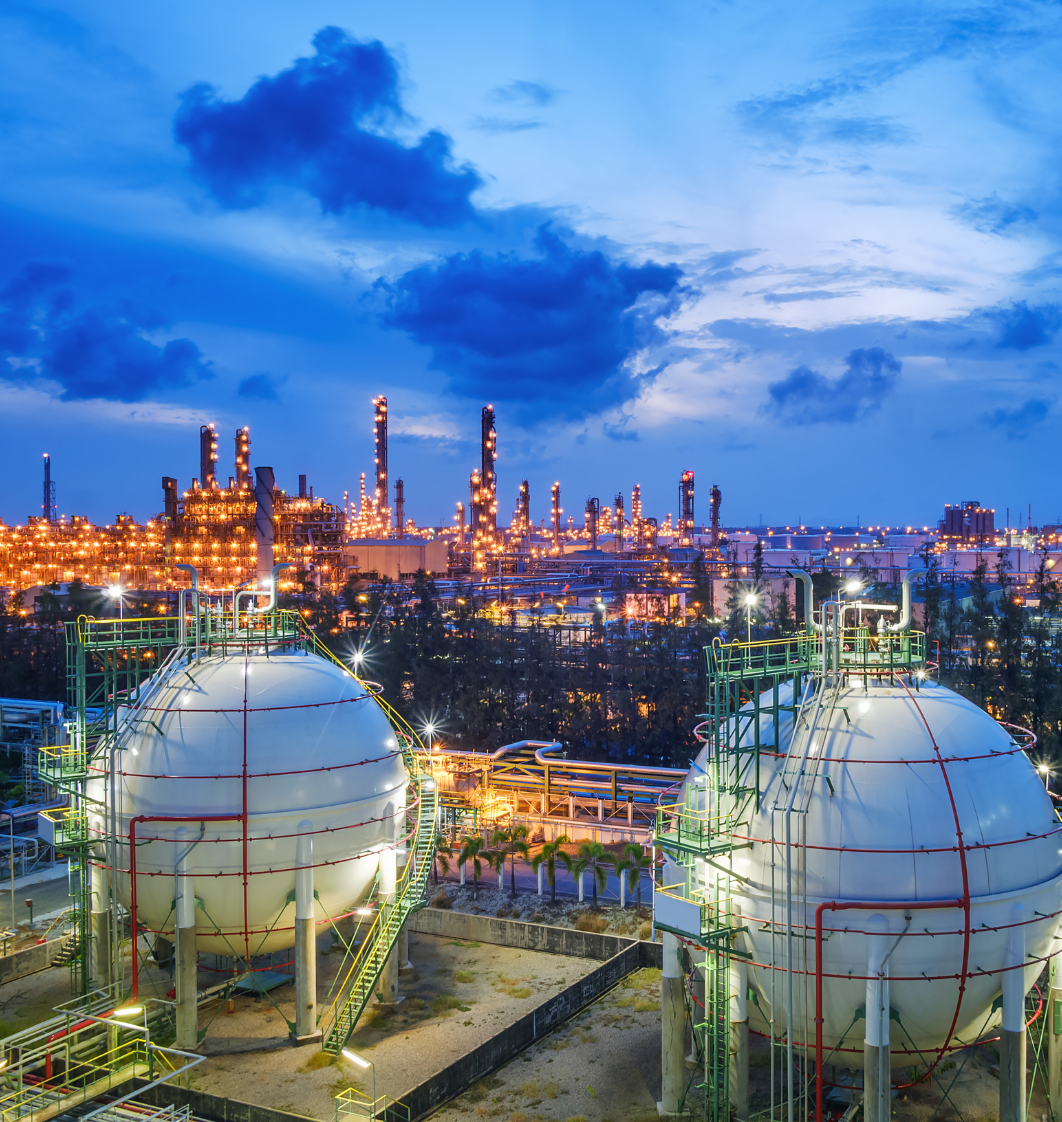

Data-Driven Reliability
Don’t waste data, use it.
Our data-driven reliability framework ensures the right data is fueling the right intelligence, helping you make confident, strategic decisions.
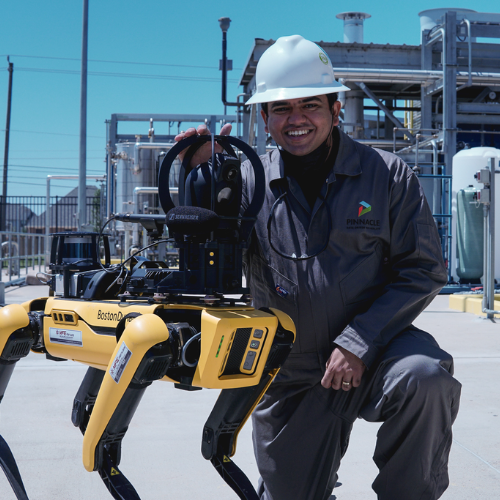
Data Collection
Collect and store the right data with quality and efficiency.
Trusted data is the foundation of a strong reliability program. Today, many data collection processes are time-consuming and vulnerable to human error, making it difficult to scale data-driven initiatives. The key to trusting your data is knowing where to leverage technology to automate processes with appropriate human oversight.
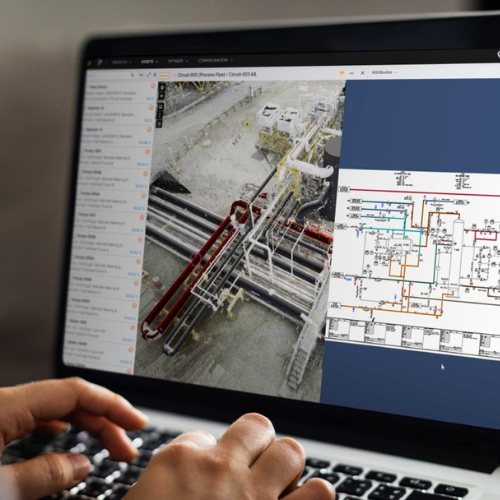
Data Organization
Build relationships between your data systems to make your data useful.
Without context and structure, data is useless. The data we use today is often static and stored in siloes, requiring abundant human intervention and assumptions to finalize any analysis. Converting raw data into digitized and connected data across your facility is critical to scaling data-driven initiatives.
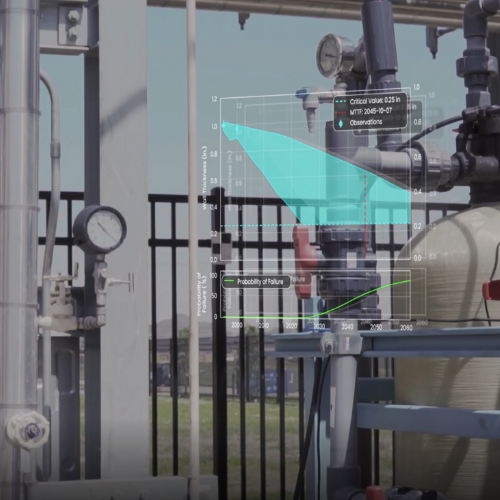
Intelligence
Drive reliability with the right data science and engineering models.
Today, many reliability models rely too heavily on subject matter expertise or data science algorithms. While these approaches can add significant value individually, they are often too resource intensive or require significant quality review. The key to improvement is knowing when to leverage data science, human expertise, or a hybrid of the two to model reliability scenarios effectively.
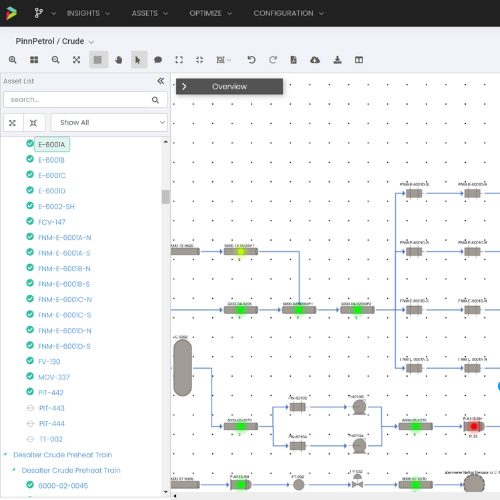
Strategic Decisions
Understand the impact of your decisions on the reliability of your facility in real-time.
Improving and sustaining the reliability of your facility is complicated. We often have to balance competing initiatives and make quick decisions without understanding their impact. Having the confidence and clarity that your decisions will positively impact your facility is critical to sustaining and improving your reliability performance. Explore the decisions a data-driven approach unlocks.
Learn about the impacts of Data-Driven Reliability
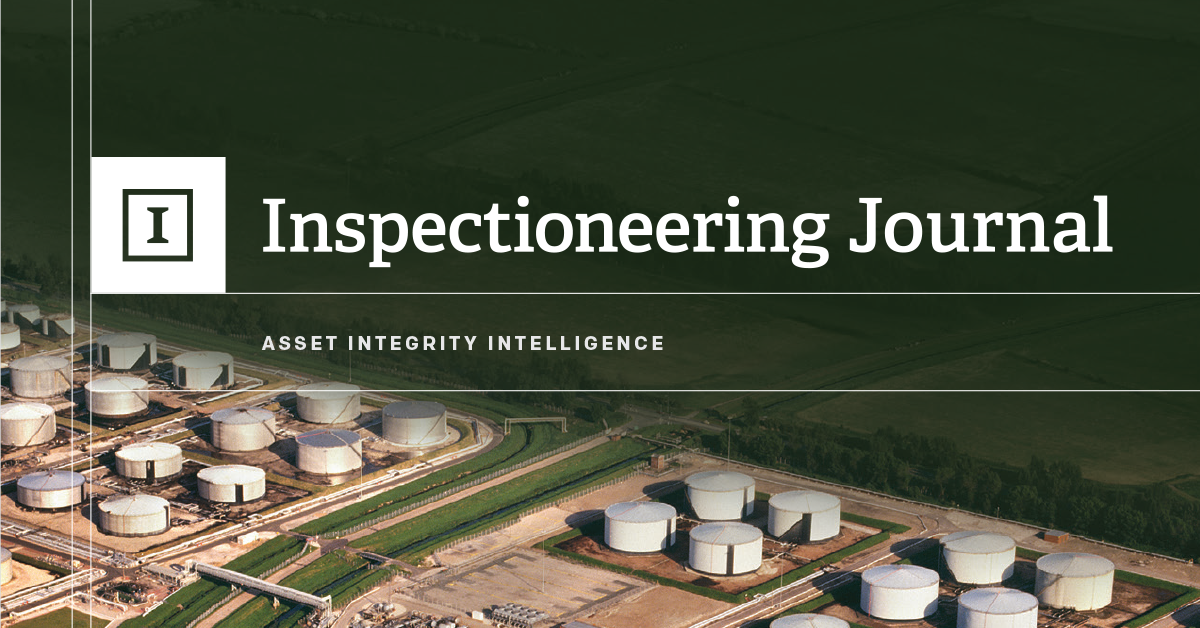
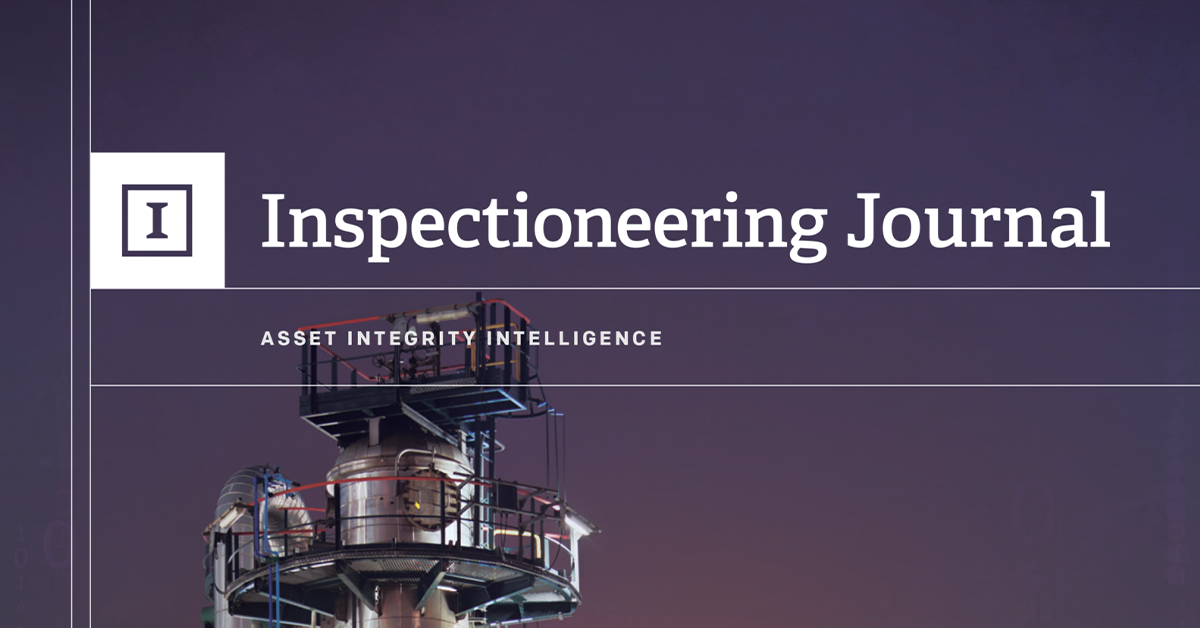
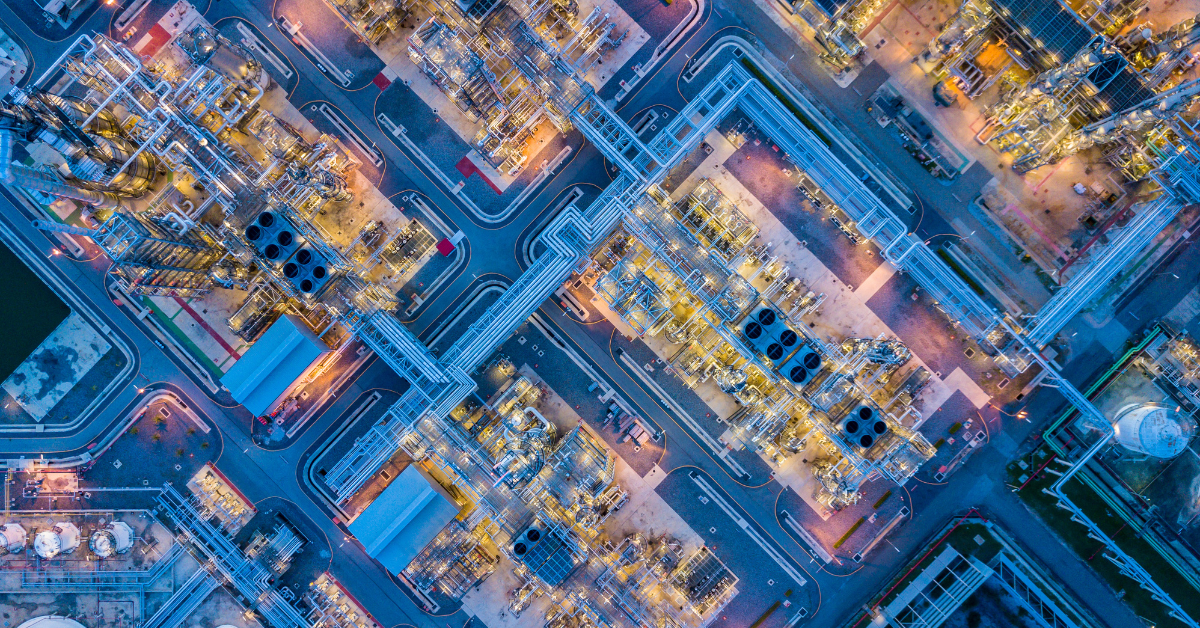
Case Study
Supermajor Uses QRO to Predict 94.22% Availability and Associated HSE Risk, Using Model to Drive Benefit-to-Cost Design and Maintenance Optimization
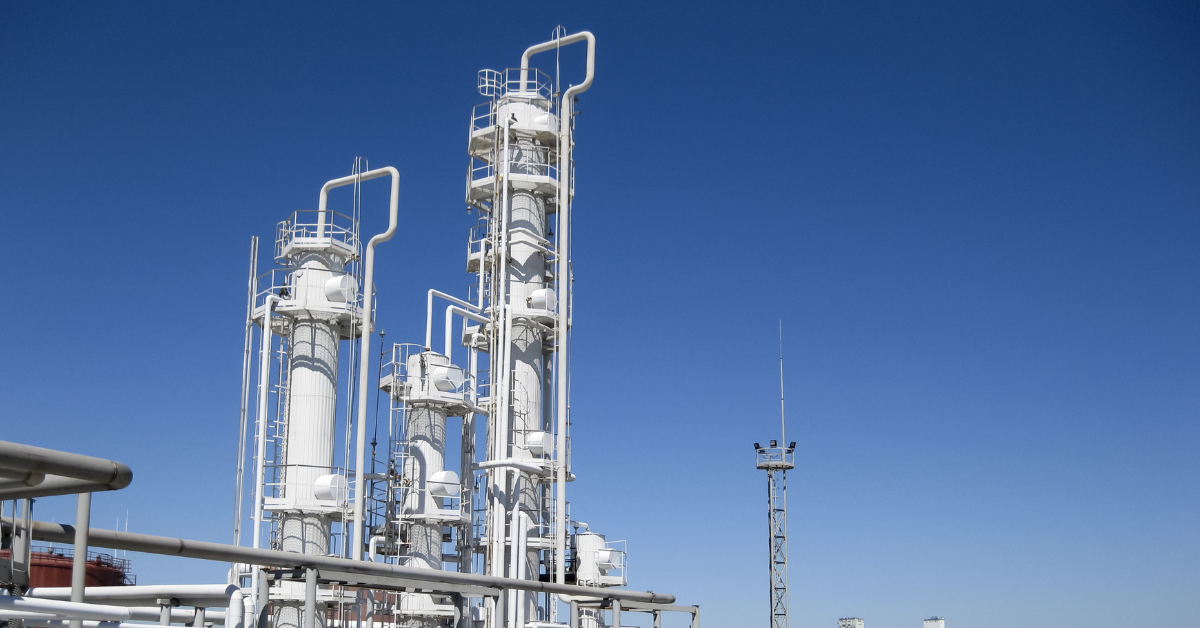