Pressure Relief Devices (PRDs) play a critical role in preventing overpressure events that can result in loss of containment, equipment damage, and unplanned downtime for pressure vessels, boilers, and other pressurized systems. Knowing which PRDs present the greatest risk to your facility and how often they need to be inspected is critical to mitigating the risk of PRD failure.
Pressure Relief Device Risk-Based Inspection (PRD RBI) is used to assign risk to PRDs based on probability of failure (POF) and consequence of failure (COF) calculations and can help your facility adjust its inspection intervals and resource allocations based on this calculated level of risk. However, despite the multitude of benefits PRD RBI provides, this approach has not been easily adopted by the industry due to its complexity.
Many facilities use API RP 581 methodology as a starting basis for PRD RBI. However, existing API 581 RBI PRD calculations are inconsistent, challenging to interpret, and contain errors. To address these concerns, we developed a tool with model improvements to the calculations. Additionally, the proposed updates to these calculations were submitted and accepted by the API RP 581 subcommittee and will be included in the Fourth Edition release.
Learn more about the project that resulted in the development of the tool below.
Common Industry Challenge
A refinery historically inspected its PRDs on time-based intervals that generally occurred every 5 to 10 years. With all PRDs on a fixed interval inspection program, the facility exposed themselves to higher risks, costs, and missed opportunities due to not inspecting some valves enough and over-inspecting others. Additionally, the fixed interval program led to unnecessary constraints in turnaround planning.
To combat these challenges, facility leadership decided to switch to an RBI approach for its PRDs. Implementing this type of approach would help the facility lower its costs and better understand how it could decrease the risk of failure. Additionally, a risk-based approach would help the facility extend its inspection and test schedules to better align with its turnaround schedule, as appropriate.
The refinery collaborated with our team to implement RBI intervals for its PRDs. The team leveraged API RP 581 RBI calculations for PRDs and found that the existing calculations contained multiple errors and the documentation was difficult to follow.
Additional issues included:
PRD Inspection Updating:
The current approach calculated incorrect risk results. For example, a B-level inspection for a PRD produced lower risk than an A-level inspection. Additionally, the approach showed lower risk for PRDs that did not get inspected than those that had any level of inspection. There was a need to modify the approach so that the confidence in the PRDs’ condition would be debited and credited, as appropriate, and that the risk was correctly calculated, correcting for the inspection and no-inspection cases.
PRD Component Probability of Failure (POF):
The current API 581 equation for component POF applies to PRDs with a design margin of four. This introduces error for assets with differing design margins.
Damage Adjusted Component POF:
The damage factor and POF are calculated at the normal operating pressure. The current probability of failure on demand (POFOD) calculation needed to be modified to allow for various design margins as well as limit the POF to a maximum of 1. This equation for PRD-protected component POF assumes that the component’s POF is constant over time and adjusts the POF for the overpressure scenarios.
Because the facility needed a technically sound, industry-accepted approach to drive its PRD inspection intervals, our team worked with the refinery’s leadership to develop a tool that would correctly execute API 581 PRD RBI calculations.
Watch Lynne Kaley, Director of Reliability Strategy discuss how the team adjusted the API 581 PRD RBI calculations to rank the risk of this facility’s PRDs more accurately.
Developing a Simplified Tool to Address a Complex Problem
To provide the facility with an industry-accepted approach that effectively addressed the gaps in API RP 581’s PRD calculations, Pinnacle determined the development of a tool that better calculated the POF and COF of the facility’s PRDs while establishing credible inspection periods was required. The tool took approximately four months to create and three months to validate with the facility.
The development of the tool required translating and programming the document logic in API RP 581 so that each intermediate step of the calculation could be analyzed and transparent to the facility. Making the results of every intermediate step visible was crucial in determining which steps were causing erroneous results. The tool now ensures that each step of the PRD RBI process makes sense and can be seen by facility personnel. Additionally, the tool:
- Modifies the level of inspection confidence factors and adds ineffective confidence factors.
- Adjusts component POF based on the assigned overpressure for each damage case. For the POFOD equations, the tool corrects dimensionless design margin factors and limits the component POF to a maximum of 1. The POF equation can be modified to accommodate different design margins instead of only being accurate for the most common design margin of four. The design margin factor extends the use of this equation to any construction code year and design margin.
- Combines two separate calculations, one with and one without inspection history, for POFOD which reconciled the API RP 581 calculations.
After the risk and inspection planning results were tested, the recommended updates to the calculations were submitted to API. These changes were balloted, accepted, and will be reflected in the Fourth Edition release. To the best of our knowledge, this tool is the only RBI tool that leverages the corrected API 581 calculations for PRDs. Depending on the number of PRDs in a study and quality of facility data, a pilot can be completed in one to four months for most facilities.
How Did the Tool New Tool Impact the Facility’s Risk Results?
By using the new tool to conduct PRD RBI, the refinery was able to review risk results and pinpoint the variables that were driving the risks for its PRDs. For example, the refinery was able to determine, document, and verify the low risk associated with the PRDs protecting its equipment in water services. Having the ability to pinpoint this risk enabled the refinery to identify issues and causal factors, and ultimately, determine the optimal timing and actions needed to mitigate risks. Additionally, having the ability to confidently identify the risk associated with specific PRDs will help the facility avoid unnecessary inspections and better optimize its budget.
The below graphs are generated by the tool and illustrate how the risk of POFOD for one of the refinery’s PRDs becomes more accurate as updates to the calculations are implemented.
Figure 1 shows the POFOD for different scenarios and illustrates how the original API 581 RBI PRD calculations incorrectly assign a “no inspection” scenario (illustrated by the navy-blue line) with a lower risk than scenarios where inspection credit should have been assigned.
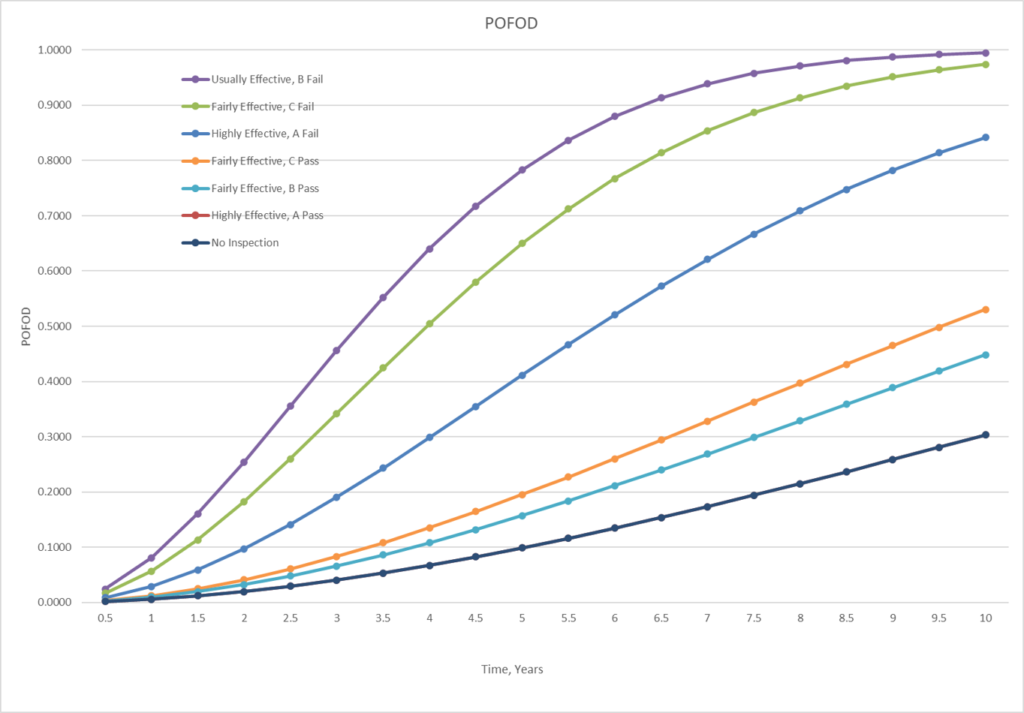
Figure 2 illustrates the impact that updating the calculations had on the PRD’s POFOD as the team developed the tool, specifically to the “ineffective” inspection scenario. In this figure, the “no inspection” scenario has been re-assigned a higher risk and labeled as “ineffective modified” (illustrated by the dark green line).
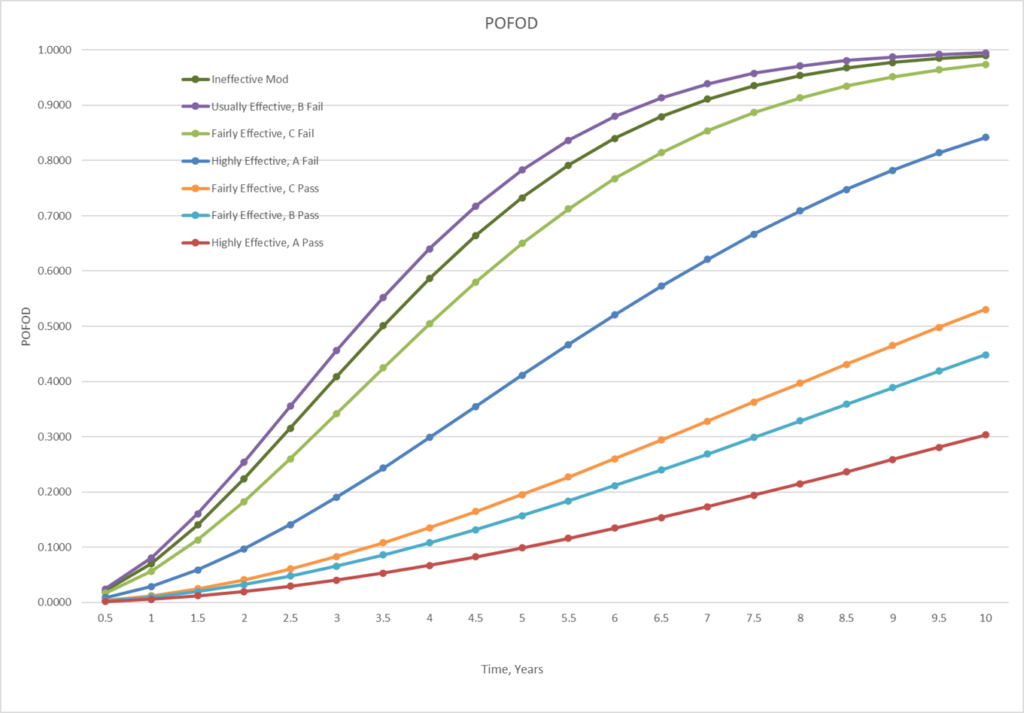
Figure 3 shows the calculated risk after the tool was completed. The “ineffective modified” inspection scenario is correctly assigned a higher risk of POFOD followed by a “Fairly Effective, C Fail” scenario.
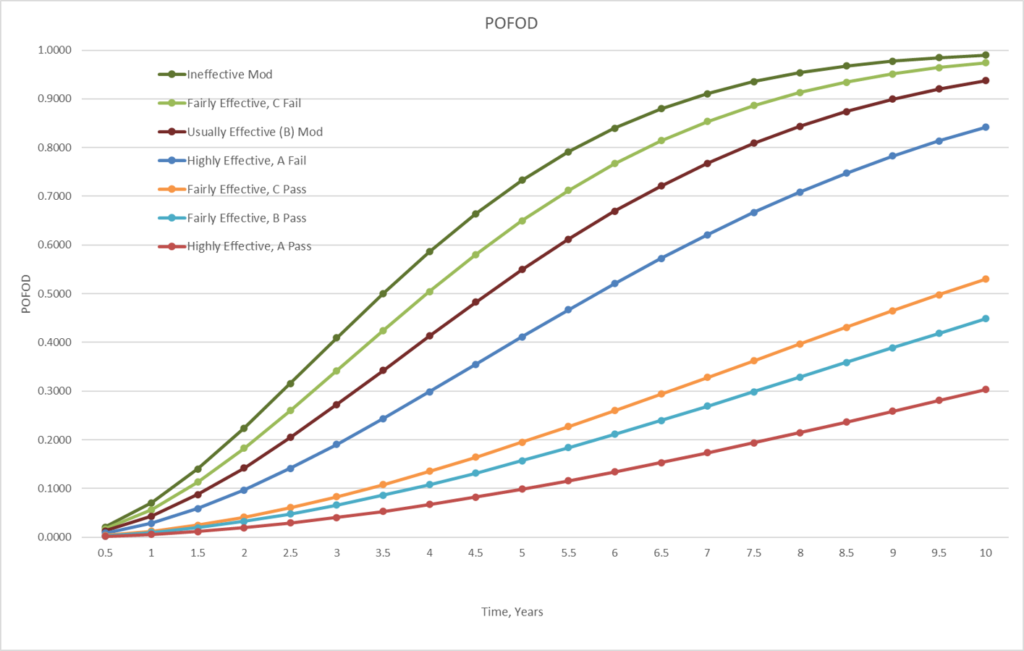
Conclusion
With a new risk-based inspection (RBI) tool for PRDs, facilities can now have the ability to calculate the POF and COF of PRDs with greater accuracy. PRDs that do not get inspected are now penalized for not having an inspection completed and show a greater risk of failure than those that had any other level of credible inspection. Additionally, the PRD calculations now apply to PRDs with a variety of design margins and POFOD is set to a maximum of 1, allowing this methodology to be applied across a variety of assets across facilities.
Learn more about how this tool can help you set more appropriate intervals and deploy your resources more effectively through PRD RBI.
Stay in the know.
Providing data-driven insights, perspectives, and industrial inspiration from the forefront of the reliability transformation.