At the end of the day, Corrosion Under Insulation (CUI) is preventable if insulation is installed and maintained properly. In industrial facilities where piping, vessels, and equipment are exposed to harsh environments, corrosion is an ever-present threat. Metal components can be attacked from both sides of the wall. Internal processes can vary between aggressive and inert, but the external environment will always have oxygen and the potential for moisture and when moisture becomes trapped beneath insulation materials it leads to accelerated corrosion of metal surfaces in the form of cracking and general thinning.
CUI is such a common issue that the American Petroleum Institute have created a recommended practice, API RP 583, just for guidance on how to manage it. In this blog, we will explore the intricacies of CUI, common issues associated with it, and opportunities to prevent it in industrial settings.
CUI is particularly challenging because it often remains undetected until significant damage has occurred and is a threat to the mechanical integrity of a facility’s assets.
Common Issues Seen with CUI at Industrial Facilities:
The advancement of technology has led to the development of sophisticated solutions, such as automation, artificial intelligence, and data analytics. However, technology alone is not the silver bullet for solving industry challenges. Yes, technology plays a critical role in finding efficiencies, but a holistic approach that leverages both technology and human intelligence is needed to fully recognize results.
Insulation Degradation
One of the primary concerns with CUI is the degradation of insulation materials. Moisture infiltration compromises the integrity of the insulation, rendering it less effective in providing thermal protection. This leads to increased energy consumption and decreased process efficiency. Furthermore, the moisture can promote the growth of mold and fungi, posing health risks to personnel. This is common in situations where insulation is installed in conjunction with heat tracing on an asset. Degradation does not just affect the insulation itself but can also include the sealants, coatings, and metal casings that protect the insulation and asset to outside exposure.
Accelerated Corrosion
CUI significantly accelerates the rate of corrosion compared to that of uninsulated piping. The trapped moisture creates a corrosive environment by forming an electrolyte between the metal surface and the insulation material. This electrolyte, coupled with oxygen availability, promotes rapid corrosion. Corrosion products, such as rust, can accumulate and further contribute to the deterioration of the metal substrate.
Equipment Failure
CUI can result in severe structural damage and ultimately lead to equipment failure. As corrosion progresses, it weakens the metal, compromising its structural integrity. This can have serious consequences, including leaks, spills, and potentially catastrophic failures, depending on the equipment involved. Such failures can result in safety hazards, production disruptions, and costly repairs.
Inspection Challenges
Detecting and monitoring CUI presents a significant challenge for facility operators. The insulation layer conceals the underlying corrosion, making visual inspection ineffective, but visual inspection can still be used to identify potential damage areas or degrading caulk/sealant. Traditional inspection methods such as ultrasonic thickness measurement or radiography may not provide accurate results due to the presence of insulation. Consequently, identifying and assessing the extent of CUI often requires more advanced inspection techniques, such as specialized sensors or thermal imaging.
Maintenance and Repair Costs
Addressing CUI-related issues necessitates regular inspection, maintenance, and repair activities. Detecting and remediating CUI at an advanced stage can be considerably more expensive and time-consuming than preventive measures. The costs associated with shutting down equipment, removing and replacing insulation, and repairing or replacing corroded components can be substantial. Additionally, indirect costs arising from production losses and environmental impacts can further escalate the financial burden.
Accidental Damage
There are many situations where insulation can be damaged by various types of personnel interaction. Situations as simple as someone stepping on or knocking into the insulation or setting tools or other materials onto the insulation. A common issue occurs when a thickness inspection is required, but insulation is not fully removed leading to an inspection port being cut. If that port is not plugged and sealed properly, moisture can make its way to the asset and start to degrade.
Industry Example
A chemical facility in south Texas capable of producing over 11 million pounds of ethylene per day embarked on conducting a Retro Positive Material Identification (RPMI) project in a strategic partnership with Pinnacle. The initial field work evaluation scope was limited to piping operating below 750 degrees Fahrenheit for safety and PMI test instrumentation exposure purposes. While stripping and testing a piping system susceptible to High Temperature Hydrogen Attack (HTHA) damage, the RPMI team encountered CUI damage in addition to significant insulation damage. The facility is operating on a Time-Based Approach (TBA) and during previous damage mechanism assignments, these line numbers had not been identified as susceptible to the CUI damage mechanism based on the assigned temperature and environment.
The damage to the piping was so significant that the RPMI inspection could not be completed without additional preparation, and the findings were reported back to the facility. Through an investigation completed by the site’s reliability team, it was determined that the system was considered a cyclical service and operated at different temperatures for significant periods of time. When damage mechanisms were originally assigned, they were done so based on the operating conditions associated with a potential HTHA failure due to the associated Consequence of Failure (COF). But the site is situated in a coastal region that is highly susceptible to CUI and by only focusing on one set of operating conditions, the site ignored the potential additional damage mechanisms, putting it at unknown risk. This example highlights the importance and risks associated with proper data collection and reliability modeling. If the pipe had failed and released the HTHA service to the atmosphere, there is a high chance that it would have auto ignited and the consequences would have been catastrophic, leading to tens of millions of dollars in damage. This unit also provides feed to another local facility and would have impacted their operations as well.
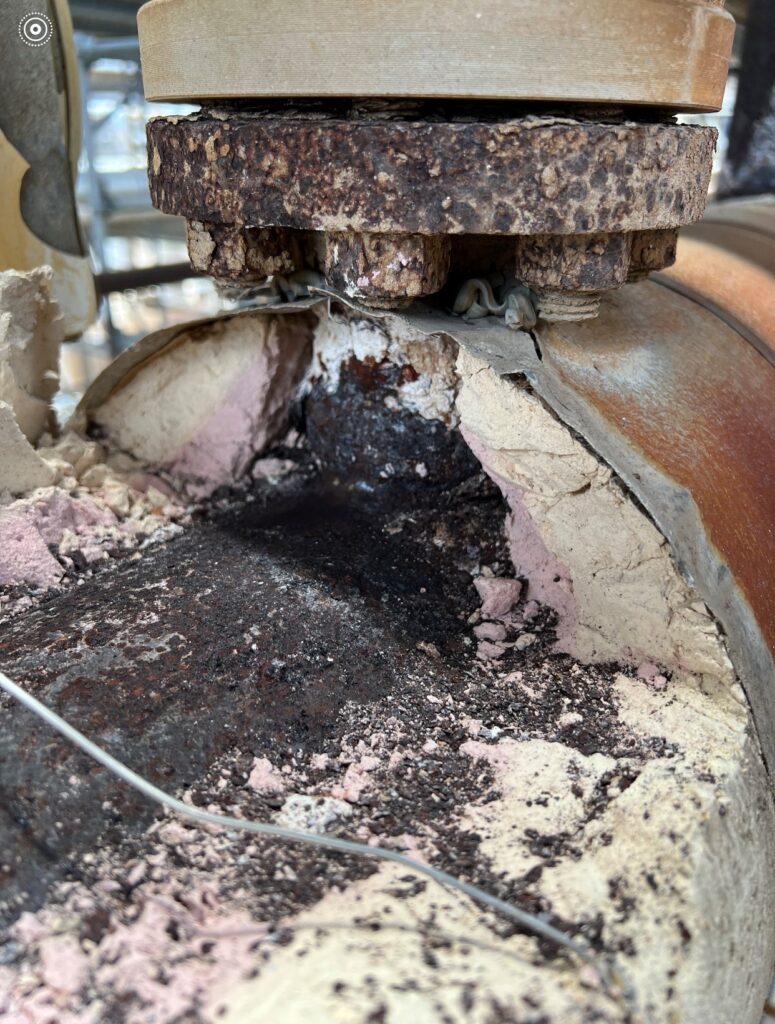
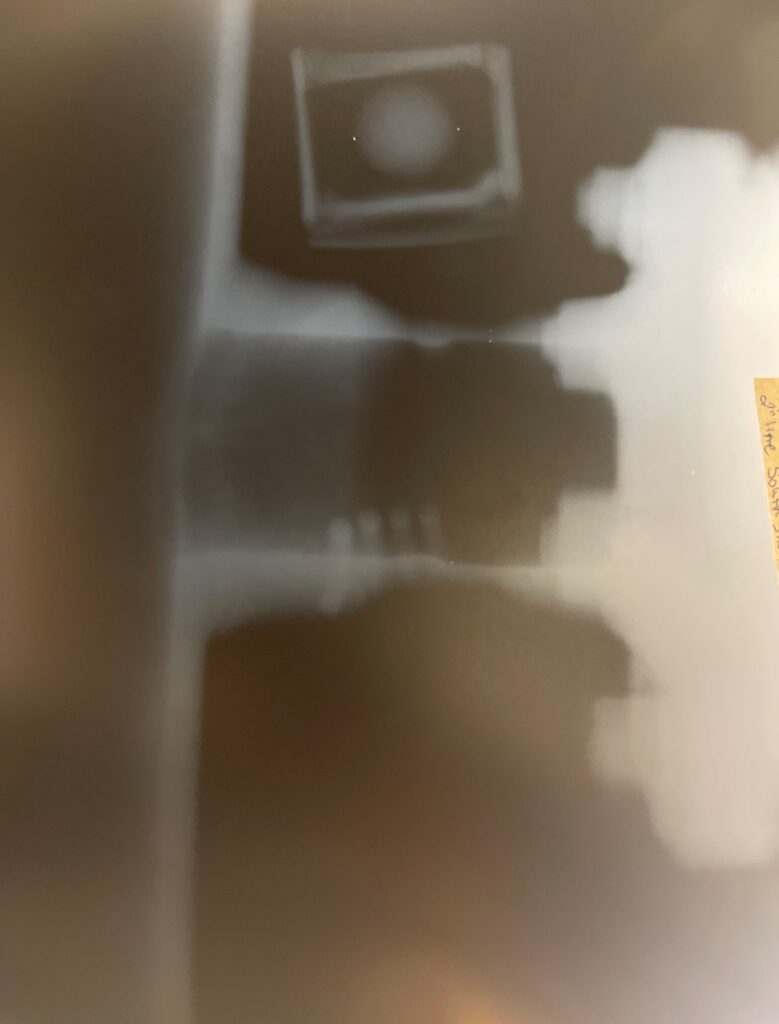
Preventing and Managing CUI
Preventing CUI requires a proactive approach that involves multiple strategies aimed at mitigating moisture ingress and creating a protective barrier for the underlying metal surfaces. Here are some effective measures to prevent CUI from occurring:
Selection of Appropriate Insulation Materials
Choosing insulation materials with low water absorption and permeability characteristics can reduce the risk of CUI. Insulation materials such as closed-cell foams, vapor barriers, or hydrophobic coatings can help reduce moisture intrusion.
Proper Design and Installation
Ensure that insulation is installed correctly, paying attention to proper weatherproofing measures. Use appropriate sealants, gaskets, and vapor retarders to minimize the potential for moisture penetration.
Insulation Maintenance
Regularly inspect insulation for any signs of damage or deterioration. Replace damaged or compromised insulation promptly to prevent moisture from reaching the metal substrate.
Moisture Control
Implement measures to control moisture ingress. This includes managing condensation by insulating cold surfaces to prevent dew point temperature variations and addressing potential sources of leaks or water intrusion in the facility.
Protective Coatings
Consider applying corrosion inhibitors or protective coatings to the metal surfaces before installing insulation. These coatings provide an additional layer of protection against moisture and corrosive agents. It is important to note that these coatings have shelf life as well and should also be inspected and reapplied as needed.
Quality Control
Ensure that insulation installation and maintenance activities adhere to industry standards and best practices. Conduct regular quality control checks to verify that insulation systems are properly installed and functioning as intended.
Advanced Inspection Techniques
Utilize advanced inspection techniques designed specifically for CUI detection. These can include non-destructive testing methods like specialized sensors, thermal imaging, or guided wave ultrasonics that can identify hidden corrosion beneath the insulation.
Education and Training
Provide comprehensive training to facility operators, maintenance personnel, and inspectors regarding the risks associated with CUI and the importance of preventive measures. Educating staff on early warning signs, proper maintenance practices, and inspection techniques can help identify and address potential CUI issues in a timely manner. It is important to educate on how CUI occurs and emphasize how easily insulation and other weather barriers, such as sealant, can be damaged or lead to CUI if not installed or taken care of properly.
Risk Assessment and Management
Conduct regular risk assessments to identify areas prone to CUI and prioritize preventive measures accordingly. Focus on high-risk areas such as equipment operating at elevated temperatures that are still below boiling point, locations with frequent insulation maintenance, or regions with high humidity.
Continuous Monitoring
Implement a system for continuous monitoring of CUI-prone areas, such as temperature and moisture sensors, to detect any deviations from normal conditions. This allows for early detection of potential CUI risks and enables prompt action.
Material Selection
One option to eliminate unnecessary CUI risks is to replace or install caging in lieu of insulation as personnel protection.
Conclusion
At the end of the day, CUI only occurs when insulation and inhibitors have not been installed or maintained properly. CUI programs can be time-consuming and expensive, and by adopting a comprehensive approach that includes proper insulation selection, installation, maintenance, and proactive monitoring, industrial facilities can significantly reduce the occurrence of CUI and safeguard their equipment and infrastructure from the detrimental effects of corrosion.
Stay in the know.
Providing data-driven insights, perspectives, and industrial inspiration from the forefront of the reliability transformation.