Achieving the Full Potential of Asset Performance Management Platforms
Inspectioneering Journal, Nov/Dec 2017 Issue
Software implementation in a business environment can be a challenging process with many pitfalls and risks. On one hand, software vendors tend to promote their solutions as the answer to all of your ills, but software users know the reality—the results often fall far short of those expectations. While the blame tends to fall on the software, it’s typically the other activities around the software implementation that were not completed that tend to have a larger effect on the success of the implementation.
Asset Performance Management (APM) software is no different. Gartner defines APM software as software that “encompasses the capabilities of data capture, integration, visualization, and analytics tied together for the explicit of improving reliability and availability of assets.” With these robust capabilities, one may ask, “why are these software implementations so challenging?”
Regardless of the software, many companies fail to realize the full potential of these robust applications. The Meridium application (recently purchased by General Electric and now referred to as “Asset Performance Management” by GE) is one example of such a platform and will provide the context for this article. As many are, it is a feature-rich asset performance management tool with potential for significant return on investment.
In my 20 years of experience of working for and with multiple companies in different industries implementing this application, I’ve observed some common themes that impede return on investment that apply to any APM software. These themes revolve around the approach to the implementation (Figure 1)—establishing a vision, recognizing and addressing data as a foundational element, optimizing asset strategies, and streamlining processes and software thru technical configuration and implementation. By focusing on these key elements, the full potential can be unlocked.
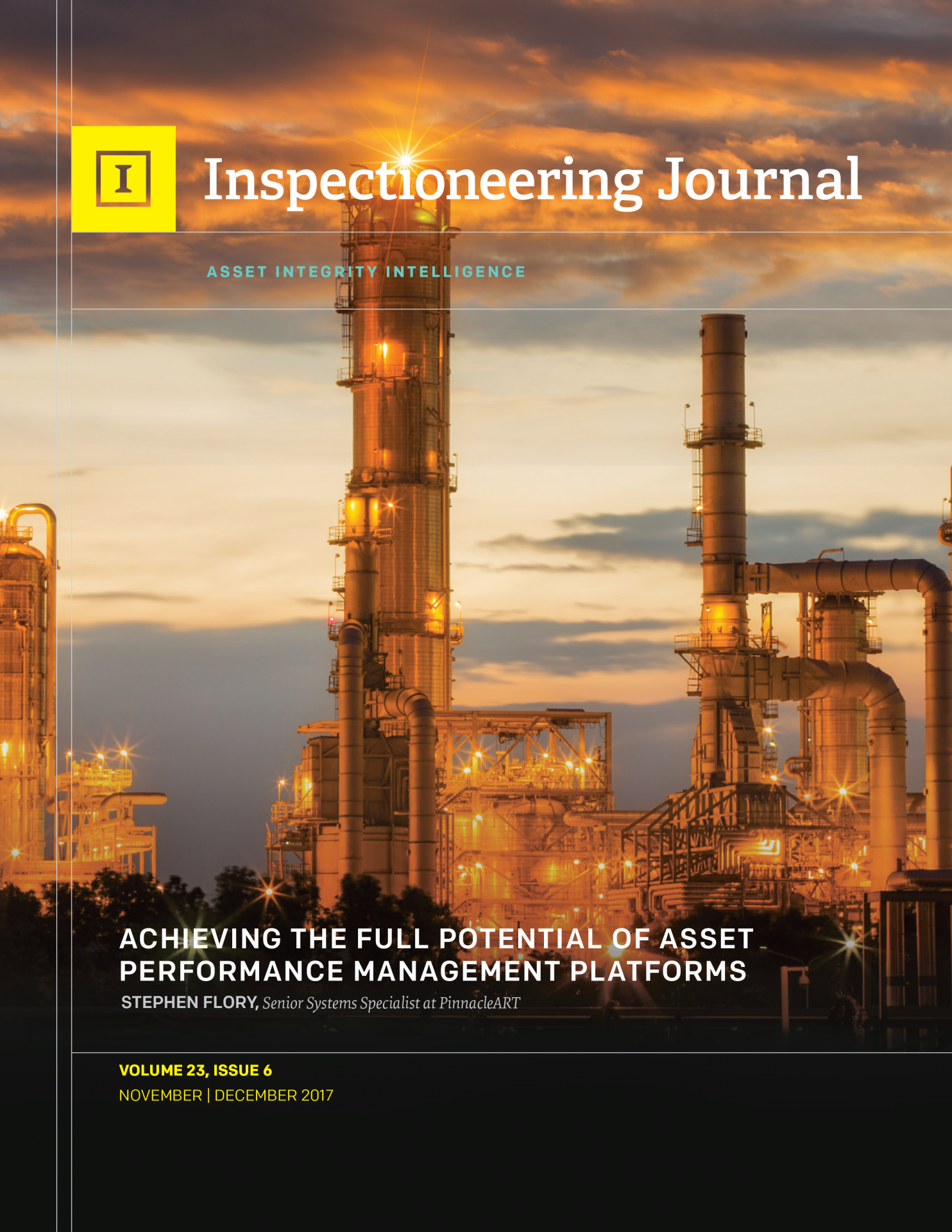
Stay in the know.
Providing data-driven insights, perspectives, and industrial inspiration from the forefront of the reliability transformation.